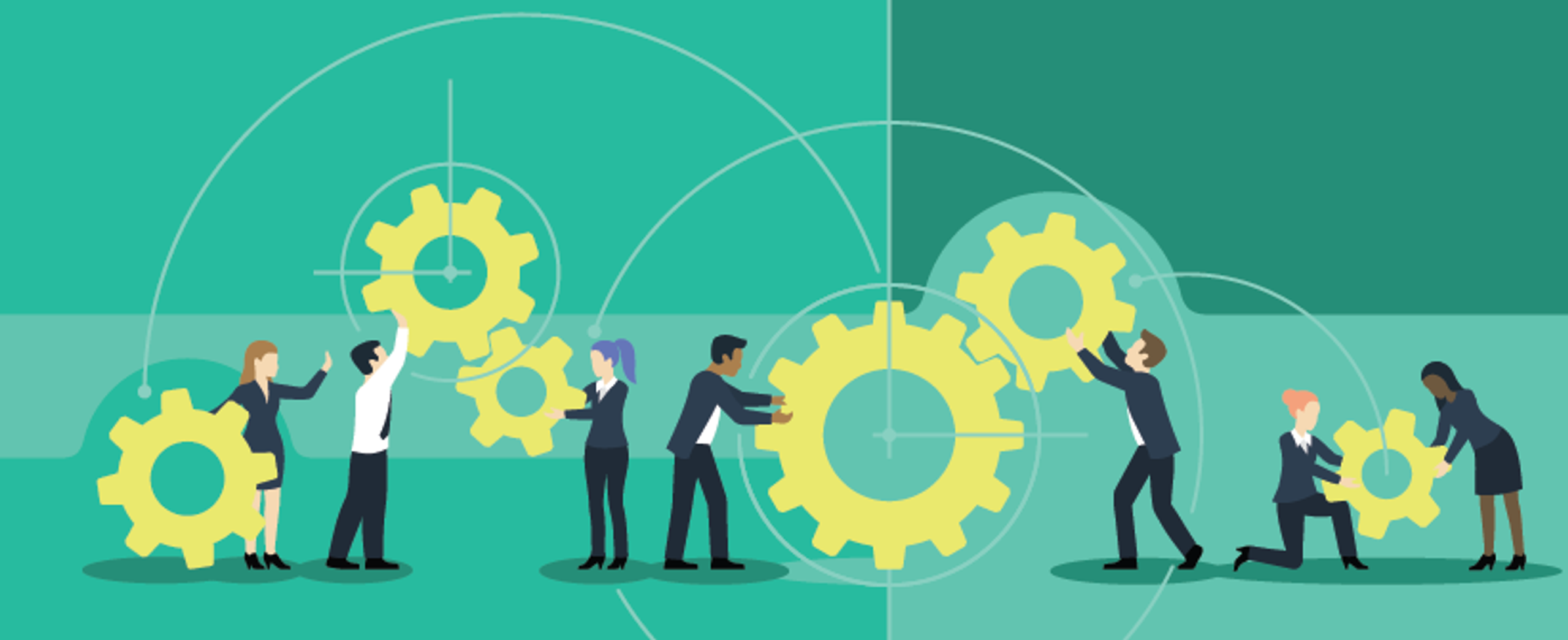
10 Common Continuous Improvement Strategies
October 22, 2024How to Choose the Right Continuous Improvement Strategy for Your Business
In the world of structured problem-solving and process improvement, there’s no shortages in methods or approaches. From Lean to Six Sigma, Kaizen to Agile, organizations today have an array of tools to choose from. The real challenge, however, isn’t in selecting the “perfect” method—because, quite frankly, there isn’t one. Instead, the key to successful continuous improvement lies in having an approach and committing to it.
It’s easy to get caught up in debates about which strategy is best or the most effective. But in reality, the most important thing is to simply have a structured process in place to guide you through identifying, analyzing, and solving problems. Whether you’re minimizing waste, reducing defects, or striving for workplace organization, what matters is consistency and an openness to learning and adapting. In this blog, we’ll explore ten proven strategies for continuous improvement that can help any organization move forward—without getting bogged down in the question of “which one is best.”
Ultimately, the best strategy is the one that fits your organization’s needs and culture, and most importantly, one that you actually use. Let’s dive into these approaches and how they can transform your problem-solving.
Kaizen – The Foundation of Continuous Improvement
Kaizen is a Japanese term meaning “change for the better” and involves everyone—at all levels—working together to drive rapid, incremental improvements. Typically applied in the Improve phase of DMAIC, Kaizen events are short, action-oriented, and designed to reorganize a process, performed by cross-functional teams to identify and eliminate waste from processes quickly (usually less than two months).
Kaizen addresses the question: “What small changes can be made today to create a better tomorrow?” Rooted in the belief that small, consistent changes lead to long-term results, it fosters a culture of continuous improvement and efficiency. To explore Kaizen’s core principles further, check out the Kaizen Tutorial for more details.
Six Sigma – Reducing Variation and Improving Quality
Six Sigma is a data-driven methodology that focuses on reducing process variability and defects to improve quality and operational performance. It leverages statistical tools and structured problem-solving techniques to identify root causes and implement effective solutions. Commonly applied using the DMAIC (Define, Measure, Analyze, Improve, Control) framework, which provides a clear roadmap for problem-solving and decision-making to improve or reinvent business processes. Six Sigma integrates with Lean principles to form a comprehensive process-improvement strategy that combines both Lean and Six Sigma techniques, as detailed in the blog A Beginner's Guide: What is Lean Six Sigma?
Six Sigma answers the question: “How can we achieve near-perfect quality and performance?” It’s ideal for industries requiring precision, such as manufacturing, healthcare, and services, especially for complex processes with strict quality standards.
Lean Manufacturing – Streamlining Operations
Lean focuses on creating value by minimizing waste and maximizing productivity within manufacturing. It streamlines operations by removing non-value-added activities, reducing cycle times, and improving flow to deliver higher-quality products and services at lower costs. Lean is most commonly applied in the Improve phase of DMAIC to identify and eliminate inefficiencies.
Lean answers the question: “How can we reduce waste and create more value with fewer resources?” It’s highly effective in environments that prioritize efficiency and minimizing waste are crucial, such as manufacturing, supply chain management, and service delivery, especially where complex workflows, excessive waiting times, or overproduction are issues.
Total Quality Management (TQM) – Developing a Culture of Continuous Improvement
TQM is a comprehensive approach involving all employees in maintaining high standards by continuously refining processes, reducing errors, and enhancing customer satisfaction. It focuses on embedding quality into every aspect of operations and is applied throughout the entire project lifecycle to ensure quality is built into each phase.
TQM helps answer: “How can we ensure quality is integrated into every step of our operations?” It’s particularly effective in organizations prioritizing long-term success through customer-focused quality management. It is ideal for industries where process consistency and customer satisfaction are critical, such as manufacturing, healthcare, and services.
PDCA Cycle (Plan-Do-Check-Act) – A Systematic Approach to Problem-Solving
The PDCA Cycle, also known as the Deming Cycle, is a four-step continuous improvement model: Plan (identify the problem and create a strategy), Do (implement the plan on a small scale), Check (analyze results), and Act (take corrective actions). PDCA helps refine processes, address inefficiencies, and test changes on a small scale before broader implementation. The PDCA cycle provides a continuous feedback loop to drive ongoing improvement efforts.
This cyclical approach answers the question, “How can we continuously improve and adapt our processes?” It’s ideal for starting new projects, refining processes, and promoting data-driven improvements.
Root Cause Analysis (RCA) – Identifying Underlying Problems
Root Cause Analysis (RCA) is a systematic problem-solving approach used to identify and eliminate the underlying causes of issues to prevent recurrence. RCA utilizes tools like 5 Whys, Fishbone Diagrams, and Pareto Charts to pinpoint root factors. For more information on performing RCA, including steps like planning, data collection, analysis, and implementation, visit our Root Cause Analysis toolbox page.
It is often used in the Analyze phase of a DMAIC project to answer: “What is causing this problem, and how can we prevent it?” RCA is ideal for implementing sustainable improvements that enhance process efficiency, customer satisfaction, and overall performance.
Benchmarking – Learning from the Best
Benchmarking is a performance measurement tool used to compare an organization’s processes, products, or services against industry leaders to identify performance gaps and areas for improvement.
It helps answer the question: “How do we measure up to the best, and where can we improve?” Benchmarking is commonly applied during the Measure and Analyze phases of DMAIC to adopt best practices and implement strategies that drive sustainable growth.
5S Methodology – Organizing for Efficiency and Safety
The 5S methodology is a systematic, common-sense approach focused on improving visual control and enhancing safety in the workplace. 5S stands for five Japanese words governing workplace organization and housekeeping: Sort (remove unnecessary items), Set in Order (arrange needed items), Shine (clean and inspect), Standardize (establish best practices), and Sustain (maintain discipline). Effective in environments prioritizing safety, efficiency, and visual management, it applies across both manufacturing and service industries.
Often used in the Improve phase of DMAIC, 5S answers the question: “How can we create a visually organized, safe, and efficient workspace?” For more details, explore our 5S Tool page.
Value Stream Mapping (VSM) – Visualizing Process Improvements
Value Stream Mapping (VSM) is a visual tool that analyzes the flow of materials and information needed to deliver a product or service, identifying both value-added and non-value-added activities. Typically used in the Define and Measure phases of DMAIC, VSM answers the question, “How can we improve process efficiency and eliminate waste across the entire value stream?”
It visualizes the current process, pinpoints inefficiencies, and outlines a future-state process with a clear action plan. Originally seveloped in the Toyota Production System, VSM and commonly used in lean manufacturing, VSM is valuable across industries for reducing waste and increasing efficiency. Learn more about VSM and its wide-ranging applications.
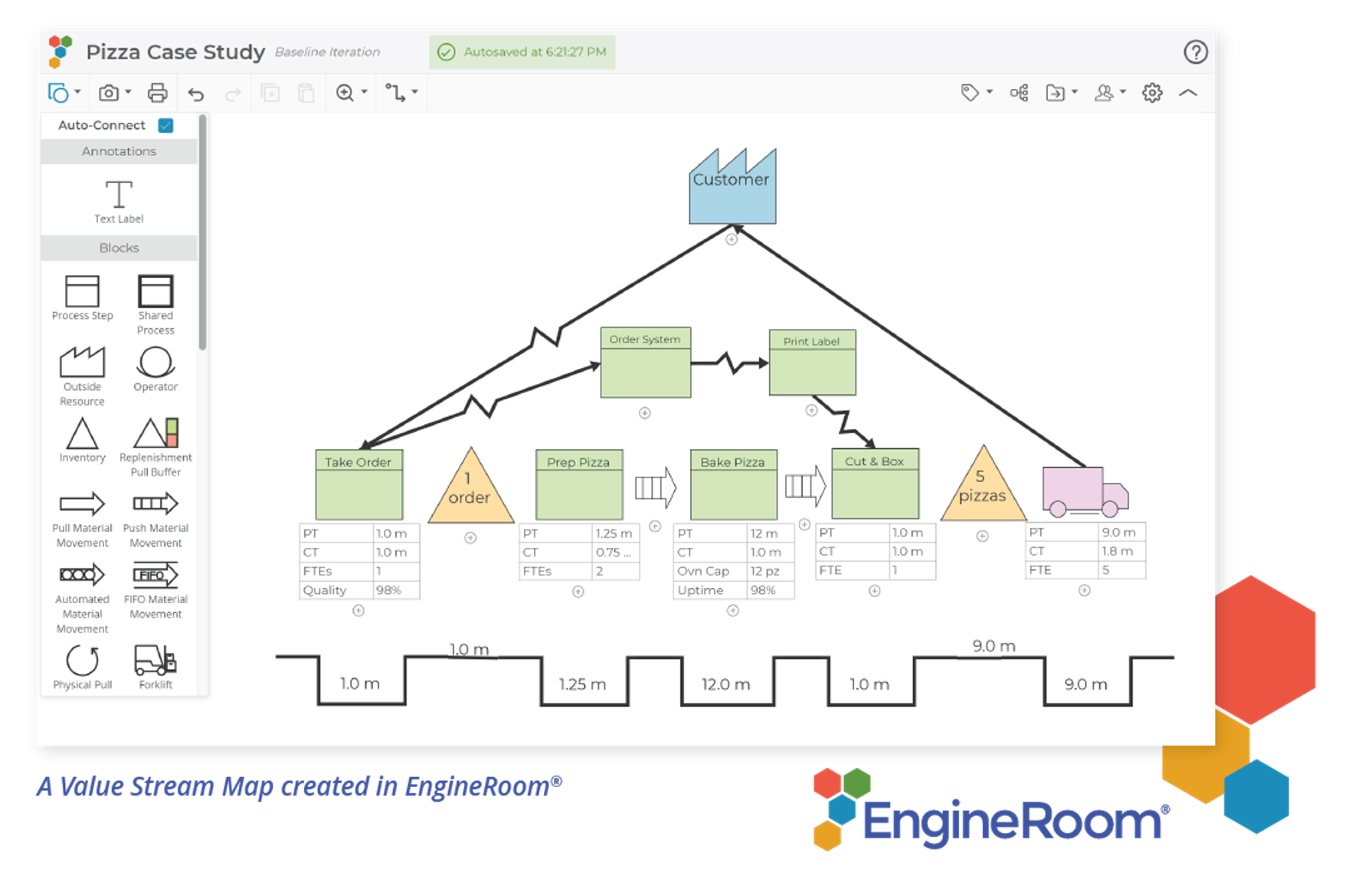
Agile Methodology - Adapting to Change
Agile Methodology is a flexible approach to project management that delivers high-quality results faster through small, iterative improvements. It emphasizes collaboration, adaptability, and continuous feedback using frameworks like Scrum and Kanban to break projects into manageable sprints.
Agile is often used to answer: “How can we quickly adapt to change and continuously deliver value?” It’s ideal for dynamic environments like software development and product innovation, where flexibility and rapid iteration are crucial.
Which Strategy is Right for You?
You might be wondering, “How do I know which strategy to use?” The answer depends on your goals and challenges. These methodologies can work together and be tailored to meet your organization’s unique needs. According to the Lean Roadmap, the real key to success isn’t about choosing the “perfect” strategy but rather committing to a structured approach that fits your culture and news. Start small, experiment, and watch as your organization moves closer to a culture of excellence—one improvement step at a time.
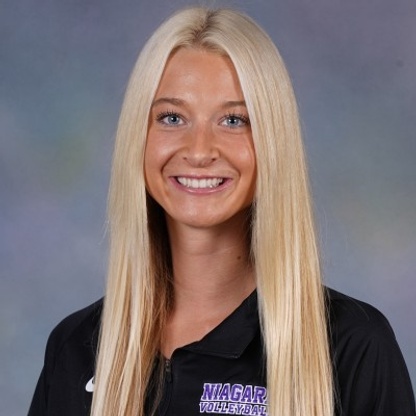
Marketing and Business Development Specialist • MoreSteam
Lexi began working with MoreSteam’s Marketing team in August 2024. Since then, she has made a strong impact through email and social media marketing, content creation, and advertising efforts. She has also helped strengthen alignment between Marketing and Sales and now supports initiatives across both teams. Lexi earned both her undergraduate degree in Integrative Management and her MBA in Marketing and Analytics from Niagara University in just four years—all while competing as a collegiate volleyball athlete. She brings the same determination and adaptability from the court to her work, continuously expanding her skills and contributions.