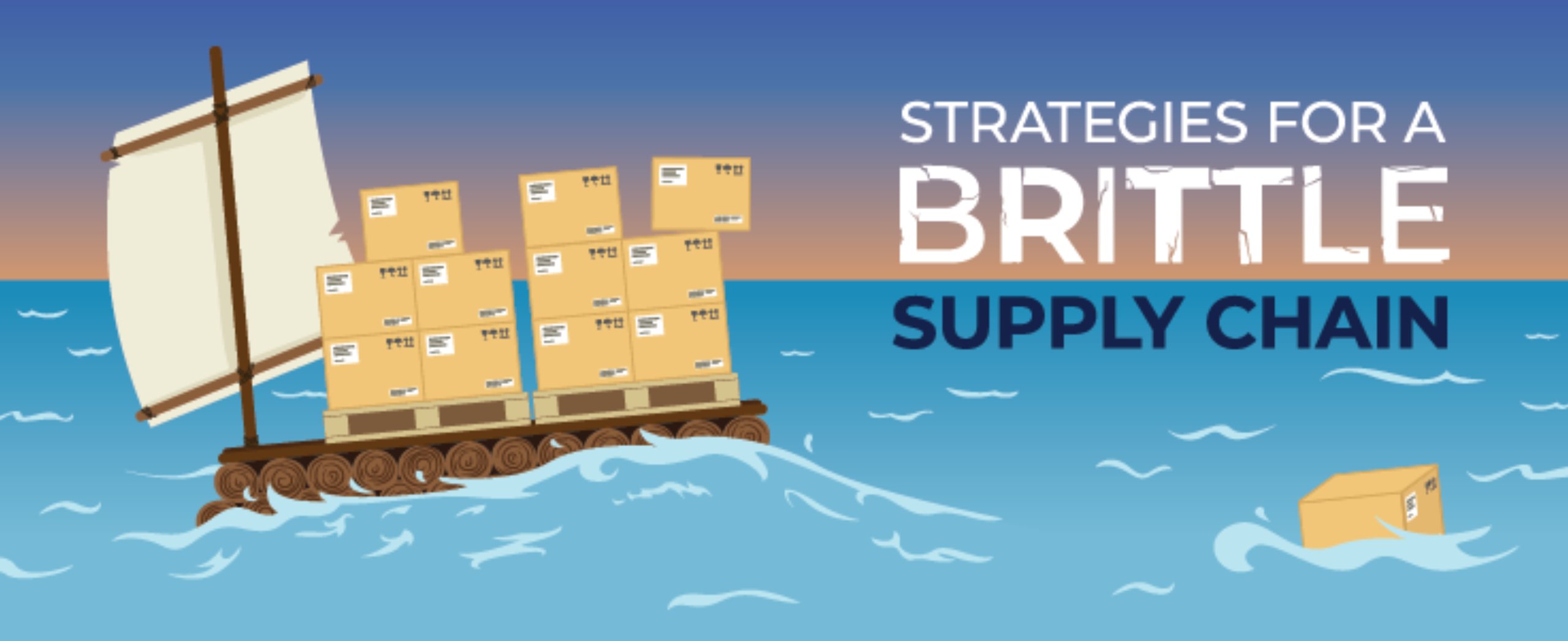
Global Supply Chain Disruptions - The Revenge of Variation
July 19, 2022Those managing complex supply chains may feel like they are trying to tow a boat cross-country with a 1977 Yugo with bald tires and a low oil light: there are too many failure modes to enumerate. Failure modes are now the common currency of any supply chain discussion, which raises the question: how have potential failure modes been considered when designing business supply chains?
Many organizations are pointing fingers at the global pandemic as a reason for the continuing supply chain complications, but a poor design is always bound to implode.
When outside factors inevitably become less stable, variation in any process design will lead to less efficient end results.
Lean methodologies and tools like 'negative brainstorming,' Failure Mode & Effects Analysis (FMEA), and Dynamic Process Modeling can help identify and manage global supply chain risks.
As outlined in several recent articles from McKinsey, MIT, and the Wall Street Journal, supply chain resilience is a hot topic. Factory supply chain problems have become all‐too‐familiar to everyone, and as we consider how to make design improvements, it's worth revisiting this design axiom, popularized by W. Edwards Deming:
Every system is perfectly designed to get the results it gets.
Our current global supply chain problems should be no surprise. The failures are a predictable output of the system. The only thing that wasn't predictable was the timing and coincident occurrence of multiple problems that have magnified the impact.
The relative stability of major factory supply chain inputs over many years allowed us to tighten the system to drive out waste continually. Lean supply chains are optimal when everything works as intended. Still, we misinterpreted relative stability as a set of conditions that would likely continue or could at least be managed instead of appreciating the fragility of a balancing act that was likely to crash. It's sort of like when my siblings and I played dodgeball in a tree. We didn't get seriously hurt, but that was luck; it was not due to a well-thought-out and resilient process design.
For many years we'd had relative political stability, demand stability, resource stability, transportation stability, and production stability. Now variation has returned with a vengeance, with full‐on FOMO, to remind us that the evil twin of stability has the power to ruin any tightly linked supply chain. With apologies to Thomas Friedman, it turns out that the world is not flat after all; there is "roundness" (variation) everywhere.
Supply chain failures have generated a new focus on making business supply chains less brittle, and you can't read anything written recently about supply chains without seeing a mention of "resilience." But what does that mean? I would say that resilience is the ability of a system to overcome obstacles and still get the job done — to absorb unplanned events, system component failures, and variation in system inputs. Building "toughened" processes that can "take a licking and keep on ticking" is the challenge of good factory supply chain design.
Two Powerful Global Supply Chain Design Tools
There are two primary design activities necessary to improve global supply chain ruggedness. The first is to fully understand potential failures (event-based "special cause" variation), and the second is to fully understand the impact of normal variation (ongoing "common cause" variation). By understanding these sources of risk, design actions can be taken to ensure that the supply chain system responds favorably. Two tools that can be enormously useful for guiding risk mitigation through design are Failure Mode & Effects Analysis (FMEA) and Dynamic Process Modeling.
FMEA is a simple but powerful method to identify and manage risks. It starts by identifying the process steps and then identifying potential failure modes, like "port locked down due to pandemic quarantine." Effects of the failure are then scored in terms of severity, likelihood of occurrence, and ability to contain the problem. Comparing relative scores helps to prioritize potential risks. For example, a failure that is very severe but also very unlikely might be a lower priority than a failure of lower severity that happens with regularity.
Coming up with all of the failure modes based on experience, insight, and, hopefully, some data, is a beneficial exercise to help people think about possibilities and consequences in new ways. The scoring doesn't need to be perfect; it just needs to get people to think in fresh ways about the real risks.
Mitigating the Global Supply Chain Through Lean Approaches
One helpful approach to frame risks is "negative brainstorming," which is prompted by the question: "If we wanted the system to fail, what types of things would we do?" Here's a list of those actions that might guarantee failure sooner or later.
- Carry as little inventory as possible, assuming no variation in delivery by suppliers
- Source product from as far away as possible, based on local production costs
- Source products from countries with profound political risk
- Use ports of entry that are bottlenecked
- Complicate product offerings to compound the impact of disruptions
- Sole-source critical components for inconsequential financial gain
- Outsource critical capabilities to others
- Assume that everything happens on average, with almost no unplanned variation
- Assume that the weather will always be favorable
- Assume that customer demand will be stable or at least predictable
- Assume that pandemics don't happen anymore
After generating a list like this, you might ask: "Which of these things are we doing?" then adjust the design accordingly.
Another tool for supply chain design is Dynamic Process Modeling, which incorporates variation into the system design to build a virtual process prototype (or digital twin). These computer models allow for stress testing of different conditions or scenarios to see how the supply chain will perform under duress.
Stay Up-to-Date On Process Improvement Best Practices by Registering for a Free Webcast!
The McKinsey article referenced above makes the following suggestion: "Create and test 'what if' scenarios. Suppose you want to find out what would happen if the shift from rail to sea transport reduced the supply of vessels by 25 percent. One technique you may want to consider is building several what-if scenarios that can be tested quickly and then prioritizing and mitigating the parts of the supply chain that fail most often." That's good advice, but testing alternate what‐if scenarios quickly is not something to be done by hand; it requires a computer‐based dynamic process model. To solve that problem, MoreSteam built the Process Playground application within EngineRoom to build high-fidelity digital models that accurately reflect reality and show the impact of variation throughout a supply chain/process.
With a virtual process prototype, you can ask important questions like, "how does this process design perform under normal conditions?...or under abnormal conditions?" or "where do bottlenecks appear when demand increases by 100%?" or "what happens if shipments are trapped on a dock for 45 days?" The idea is to test before you invest and know in advance how the process will perform under adverse conditions — then develop mitigation strategies for those weaknesses.
As you build supply chain models, consider these lean design axioms:
- Variation is the root of all waste. Lean methods don't work very well when multiple process components vary
- Stability, or at least predictability of demand, and production makes everything more robust
- Visibility to all supply chain activity is critical — you can't manage what you can't see
- The shorter the lead time, the better
- Proximity makes management easier — whether virtual or physical, short distances improve visibility and decrease reaction times
- Flexible and accessible capacity provides more room for error
- Simplicity = reliability. Supply chains are like physical products: the more moving parts, the higher the probability of failure
- Inventory may be a form of waste, but not having any product to satisfy customers is far worse
- Geopolitics are getting trickier, not more predictable
That's my 2 cents.
-Bill Hathaway
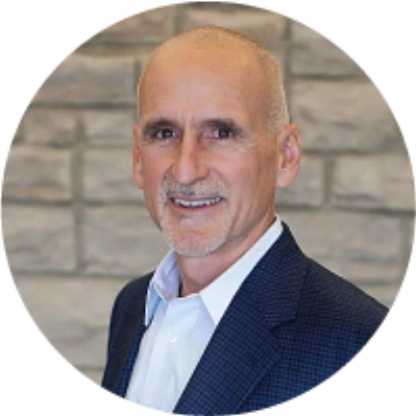
CEO • MoreSteam
MoreSteam is the brainchild of Bill Hathaway. Prior to founding MoreSteam in 2000, Bill spent 13 years in manufacturing, quality and operations management. After 10 years at Ford Motor Co., Hathaway then held executive level operations positions with Raytheon at Amana Home Appliances, and with Mansfield Plumbing Products.
Bill earned an undergraduate finance degree from the University of Notre Dame and graduate degree in business finance and operations from Northwestern University's Kellogg Graduate School of Management.