
What is Lean Thinking?
July 29, 2024‘Lean thinking’ may be an unfamiliar term, but it’s hardly a foreign concept. In fact, it’s highly likely that you have already applied Lean thinking many times without even realizing you’ve done it.
Think about each time you go grocery shopping. How do you map out the route you take through the store? It’s probably some variation of collecting the items at the front of the store first, then working your way to the back to ensure that you don’t have to turn around or double back.
Or think back to the last time you organized your basement. You have a slew of cardboard boxes and a whole lot of junk. The logical next step is to label each box and then sort your junk into the appropriate vessel. You might even take it a step further and store each box based on its importance or relevance (the box labeled “old kids toys” can probably be placed in the back of the basement, while the “extra cleaning supplies” box can sit on the storage shelf at the front).
If you haven’t already guessed it, Lean thinking is an exercise in efficiency. In many cases, our brains are hardwired to ‘think Lean’ because it’s a human tendency to want to do things better, faster, and simpler.
Lean thinking is a methodology that focuses on creating value by eliminating waste and optimizing processes. It originated in the manufacturing industry, particularly with Toyota, and was initially developed as the Toyota Production System (TPS) in the mid-20th century. Since then, Lean thinking has evolved well beyond manufacturing and is widely known and implemented across many other industries today.
But why is Lean thinking so important? And why should organizations adopt it into their practices in the first place?
What are the Benefits of Lean Thinking?
Implementing Lean thinking across your organization offers several benefits that are important to leadership and the overall function of the business. This includes:
- Operational efficiency. The concept of Lean thinking falls under the larger umbrella of Operational Excellence. It plays a part in driving operational efficiency because identifying and eliminating waste improves productivity and reduces costs.
- Customer satisfaction. No business has ever been successful when the bulk of its customers aren’t satisfied. Customer satisfaction is at the heart of Lean thinking because it prioritizes value from the customer’s perspective.
- Employee engagement. Lean thinking fosters a culture of continuous improvement and employee involvement. Engaged employees are more likely to contribute to process improvements and feel a sense of ownership in their work. In a Lean organization, employees at all levels are encouraged to identify inefficiencies and suggest solutions, leading to higher morale and a more collaborative work environment.
What are the Core Principles of Lean Thinking?
Every core principle of Lean thinking aims to minimize waste. It’s worth noting that many of these principles operate in a circular pattern rather than a linear one. Lean thinking is not a “set it and forget it” mentality; optimization happens when processes are consistently monitored and improved upon.
Value
Value in Lean thinking is defined from the customer’s perspective. It involves understanding what the customer truly wants and ensuring that every step in the process adds value to the end product or service.
Think about the last dinner party you had. After receiving a final count of guests, you probably asked the group about any dietary restrictions, allergies, or preferences. Then, you took stock of who was coming and determined how much food to buy so everyone would leave full and happy. And finally, after cooking all the food, you included some final touches that would really elevate the experience: a great table setting, some good music, and a delicious bottle of wine.
This is an example of value. You’re only including elements of this party that you know your guests will enjoy; there’s no need to add a game of charades if you know the crowd won’t be enthusiastic about playing it or a seafood appetizer to a room full of people who hate fish.
Value Stream
A ‘value stream’ is a map or outline of all the steps required to deliver a product or service to the customer. The exercise of mapping the value stream helps to visualize the process steps, timeline, and information flow in a process from start to finish. By doing so, it is easier to identify and eliminate non-value-added activities, or waste.
Consider your morning routine from waking up to leaving for work as a process. Most of us are tired in the morning and tend to establish a routine that’s as efficient and stress-free as possible. You likely prioritize and order the tasks you have to do – like brushing your teeth, showering, having breakfast, and dropping the kids off – and hiding in that process are activities that do not constitute value – like snoozing your alarm, indecision on an outfit, or searching for your keys before leaving the house.
Flow
Achieving a smooth flow of value-creating steps is essential in Lean thinking. This means ensuring that each process step seamlessly follows the previous one without delays. It’s normal for this principle to go through many iterations since determining optimal flow is often difficult without first seeing the process in action.
If you have elementary school-aged children, you're likely familiar with the daily pick-up and drop-off routine. Your school may have experimented with various drop-off methods before finding an "optimal flow." In the example below, cars were initially unloaded in a single file line in batches of five at the back of the school. This required all five cars to unload completely before the next batch could move forward. The improved drop-off process still unloads vehicles in batches of five but allows each car to leave immediately after its student exits, instead of waiting for all the cars in front to finish unloading.
Pull
The pull system is a core Lean principle that contrasts traditional push systems. Instead of producing goods based on forecasts, a pull system produces items based on actual demand. This helps prevent excess inventory, which is one of the eight wastes.
For example, if you live alone, instead of buying large quantities of groceries all at once, it makes more sense to buy only the items you need for the week. This way, you prevent overstocking, reduce food waste, and ensure you have fresh ingredients for your meals (in addition to saving money – win-win).
Perfection
Lean thinking emphasizes continuous improvement and the pursuit of perfection. And while it might feel unrealistic to think that an organization can be perfect, it’s not necessarily about achieving perfection. It’s about continuously striving for perfection. Organizations should consistently refine their processes and look for the best ways to eliminate waste and enhance value.
This core principle can apply to any hobby, sport, or job you picked up and stuck with. This year, I picked up sewing. And the first garment that I made was nothing short of terrible. But I could pinpoint where I went wrong when I looked at all my mistakes. So I started over, making the same garment again, this time with process changes. The second time around, it still wasn’t perfect, but it was much better. And the third time I made it, it was even better. Pursuing perfection isn't about never making mistakes; it's about learning from mistakes and using them to improve each time.
How Do You Implement Lean Thinking?
As we have acknowledged above, everybody is inherently capable of Lean thinking, and most of us have already applied it at some point in our daily lives without realizing it. Implementing it across an organization and encouraging a culture of continuous improvement takes a little practice, but the hard part is already done. Most people will already know how to. The real work is getting them to adopt the mindset of practicing it consistently. A culture of continuous improvement means teaching everyone how to approach every problem through a Lean lens.
Leadership should familiarize every employee with a few simple elements before implementing Lean thinking.
Identifying Wasteful Practices. As mentioned, organizations should first identify any wasteful practices in their processes. There are eight types of waste, including defects, overproduction, waiting, and unnecessary motion.
Encourage your whole team to start identifying these wastes by taking them on a Gemba walk, setting up weekly check-ins, and creating an atmosphere of open and trustworthy communication between all levels of employees.
Tools and Techniques. Lean thinking is accompanied by various tools and techniques to help organizations implement its principles. Kanban, for example, is a visual tool that helps manage workflow and inventory. The 5S methodology focuses on workplace organization to enhance efficiency and safety. Kaizen encourages small, incremental changes that collectively lead to significant improvements.
Cultural Change. A successful Lean implementation requires a cultural shift within the organization. It might sound simple, but this is often the most challenging step. Humans are hardwired to do things how they’ve been taught (or how they prefer to do them) and stick to it. Changing someone’s mindset around how they perform their work takes a lot of time, patience, and persistence. It’s imperative to engage employees (and leadership) in Lean practices consistently. Make sure you are providing training, encouraging open communication, and rewarding contributions to process improvements. Leadership must champion Lean principles and lead by example to inspire employees at all levels to embrace the change.
Lean thinking offers a powerful framework for enhancing efficiency, improving customer satisfaction, and engaging employees. Implementing it across an entire organization may take time and effort, but it lends itself to an exercise that can start small and grow as employees become more accustomed to it. And encouraging your company to think Lean may not be as hard as you think; after all, it’s already a mindset we use daily to drive success.
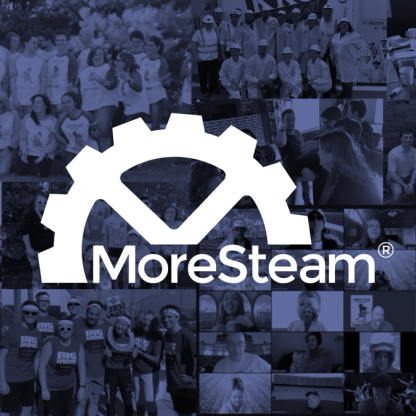
MoreSteam's Enterprise Process Improvement platform includes the tools, training, and software you need to transform your organization, large or small, into a problem-solving powerhouse. Our products are trusted by over half of the Fortune 500 and by other organizations and universities worldwide. When you partner with MoreSteam you gain a team dedicated to helping you succeed.