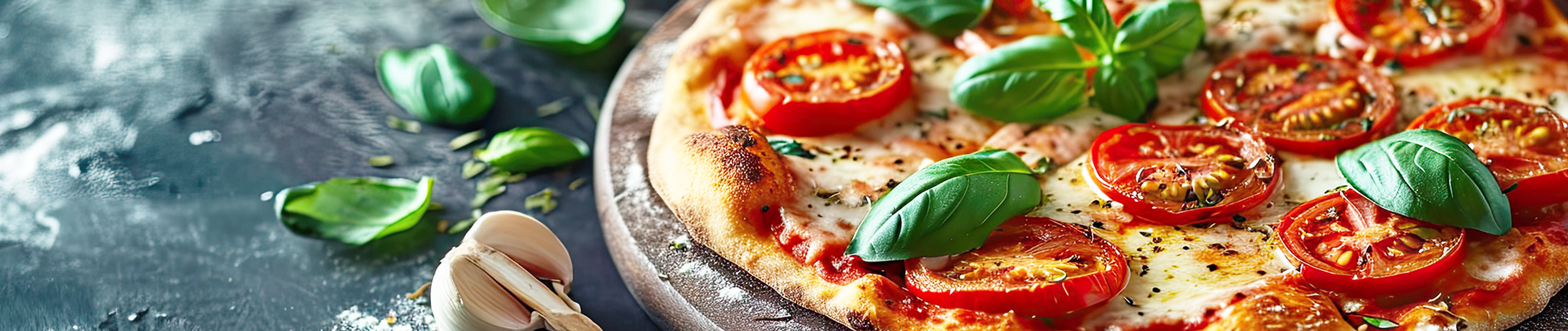
Process Modeling Produces Transformational Recipe for Success
In the bustling world of fast-casual dining, one popular pizza chain has carved out a distinctive niche with its commitment to speed, individuality, and unbeatable value. At the heart of their vibrant operation is a dedicated team of individuals striving to deliver on three fundamental customer promises:
- Fast service
- Allowing customers the freedom of individualizing their pizza
- Serving delicious food at an affordable price
However, even the most promising enterprises encounter challenges, and this chain found itself facing a significant operational hurdle. The restaurant saw extended queue times during peak eating hours, jeopardizing their customer promise of fast service.
They immediately recognized the importance of addressing this situation to maintain customer and employee satisfaction, and sought a solution to enhance its throughput and decrease the stress on their employees.
Their rapid growth was affording opportunities to open new locations, which made their dilemma particularly complex. Initially, they turned to an obvious solution: replacing the current ovens with larger ones to meet the growing demands and capacity needs. However, that would require a hefty reconstruction of every one of their existing restaurants, and it would be nearly the same cost as building an entirely new site.
So, they returned to the drawing board and approached Service Physics – a collective of experienced leaders in the service industry driven by a passion for customers and a commitment to adding value to the places where people live, work, and play. Service Physics advocates for simplicity through operational excellence, encouraging what they refer to as a "use of minds before wallets."
Approaching the Problem Presented
The Service Physics team needed to understand the current state of operations, so they started with observation and data collection.
Specifically, Service Physics wanted to answer:
- What is the current production capacity of the system?
- How much equipment capacity exists across the system?
- How much human capacity exists across the system?
They performed studies of line-off rate, machine utilization, and labor utilization to gain insight into the operation's overall health. The data they collected provided an objective view of the challenges, helping the team distinguish between the perceived and actual problems.
After initial observations and data analysis, Service Physics pinpointed three primary issues:
- Bottleneck at Expo
- Batching Problem During Oven Loading/Unloading
- Bottleneck at the Assembly Line
Armed with better information on the current state, the team at Service Physics turned to MoreSteam's online process modeling tool, Process Playground, to rapidly test improvement solutions. Process Playground enables teams to gain insights into process dynamics, identify bottlenecks, and experiment with improvements before implementing changes in a real-world setting by creating a dynamic virtual model of a process or system.
This modeling effort led to a digital twin of the pizza-making process that the chain deploys. This virtual process replica provided a highly accurate representation of the complex dynamics within the operation, capturing the nuances of customer flow, order processing, and potential bottlenecks that the team was seeing on the "shop floor." By aligning the digital twin with real-world observations, the model became a powerful tool for testing proposed solutions, identifying potential areas of improvement, and optimizing the operational workflow, all while minimizing the amount of real-world experiments.
Interestingly, utilizing the virtual process prototype revealed a strategic alternative. Contrary to the initial assumption of requiring a new oven, the team discovered that optimizing the current ovens' capacity through a restructured pizza-making process could lead to remarkable improvements.
The Service Physics team implemented "pods," or dedicated workstations for each employee on the pizza assembly line, and changed the display to ensure that customers could easily see every pizza topping available.
These changes reduced queue time by 33%, achieving a substantial increase of +16 pizzas throughput every 30 minutes. This revelation debunked the need for a new oven and demonstrated the transformative potential of optimizing existing resources. Arguably more important, validating this theory through the Process Playground model instilled confidence in the restaurant’s team before moving forward to implementation.
Now, in making these changes the Service Physics team understood that unlocking the bottleneck at the assembly line would have exacerbated the bottlenecking at the Oven and Expo stations. So, the team leveraged their work improvement methodology, ERACS, which stand for:
- Eliminate
- Rearrange
- Add/Subtract
- Combine
- Simplify
to ensure an even flow throughout the operation and a consistent wait time and service experience for the customer. Eliminating batch loading and unloading of pizzas in the oven created an even flow through the oven, allowing for greater machine utilization and throughput. Then, rearranging and reorganizing the Expo workstation (5S) and introducing simplified standard work routines reduced the workload on the Expediter so that they could keep up with the increased flow of pizzas and put more focus on their connection with the customer while delivering the final order.
The Transformative Effects of Continuous Improvement
The pizza chain’s team is now working to implement the new makeline changes and is starting the initial implementation on a smaller scale. Testing out the changes in a few select restaurants first allows for a thorough assessment and fine-tuning of the process in a controlled environment.
A crucial component of this rollout is a structured training cascade that starts with leadership. The training aims to ensure a comprehensive understanding of the new makeline structure, its benefits, and the underlying rationale for the changes. The training cascade assures that every employee knows how to make a pizza as effectively as possible when on the assembly line.
Training modules will cover various aspects, including customer interaction, navigating the new makeline structure, and utilizing Continuous Improvement (CI) tools for ongoing enhancement.
For customers, the reorganization led to a streamlined service for large orders, ensuring they no longer congested the line. The restructured process also contributed to a smoother flow, allowing customers to order multiple entrees without needing to navigate backward and forward in the line.
The ability to see all the ingredients at once empowered customers to make quicker decisions, streamlining the ordering process and contributing to an overall more efficient and satisfying experience.
Introducing "pods" in the makeline significantly reduced unnecessary motion on the employee’s side. This restructuring allowed team members to operate more efficiently and positively influenced the dynamics of the work environment.
Final Thoughts
The collaborative effort between this pizza restaurant and Service Physics offers a few incredible takeaways:
- This story is a compelling lesson in effective problem-solving; it's crucial to understand and define the problem before seeking a solution. While the initial solution seemed obvious (we need to make more pizza; therefore, we need bigger ovens to make them in), Service Physics dove deeper and sought to fully understand the current state of operations before moving to solutions.
- What started as a structured approach to problem-solving led to a more significant change: the culture. Working with Service Physics, the pizza chain’s team was able to see firsthand just how crucial it is to implement a culture of continuous improvement in their organization. They have since integrated the thinking and tools learned from their time with Service Physics.
- Process modeling allowed both teams to test ideas without disrupting the actual operation. This not only saved time and money but also empowered the team to make data-informed decisions. Process modeling is an incredibly powerful tool that has the potential to rapidly transform operations without the risk of real-world disruption.
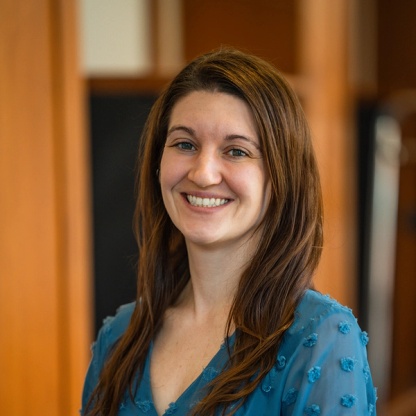
Vice President of Marketing • MoreSteam.com LLC
Lindsay Van Dyne joined the MoreSteam team in 2014. She is responsible for developing and executing the company's marketing strategy. Her marketing experience includes technical aspects of search engine optimization (SEO), digital content marketing strategies, lead generation, website development, event management, and partner relationships. Before switching to the marketing team, Lindsay spent several years as MoreSteam's eLearning product manager. During that time, she led the eLearning team through an entire UI transformation, developing a new user interface for training, expanding the language offerings significantly, and adding features like notes & highlighting and a user dashboard for training stats. Lindsay's drive and spicy personality bring a fresh perspective to the leadership and marketing teams, encouraging others to think creatively.
Lindsay received a B.S. in Chemical Engineering from the University of Notre Dame and a B.S. in Computational Physics and Mathematics from Bethel College.
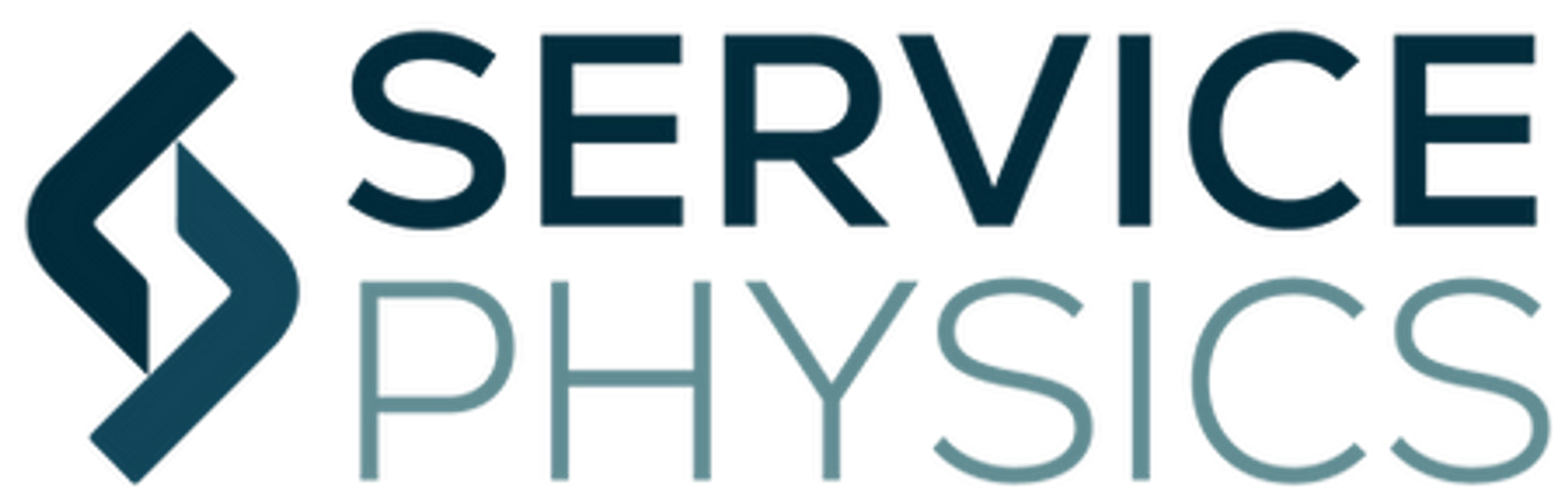
Service Physics provides data-driven operations consulting, to empower the world's largest leading hospitality and service-based brands.
13.9 million people employed in food service occupations
Sales in food service grew from $632 billion in 2012 to $898 billion in 2022 according to National Restaurant Association data.
7.27%
ESTIMATED JOB GROWTH
10-year projection
21.4%
ESTIMATED OUTPUT GROWTH
10-year projection
Process Modeling Resources
- What is Discrete Event Simulation (Process Modeling)?
- Learn Modeling with Kathy's Best Wursts Follow-Along Case Study
- Using Modeling to Teach Lean Six Sigma
- Modeling Bakery Operations