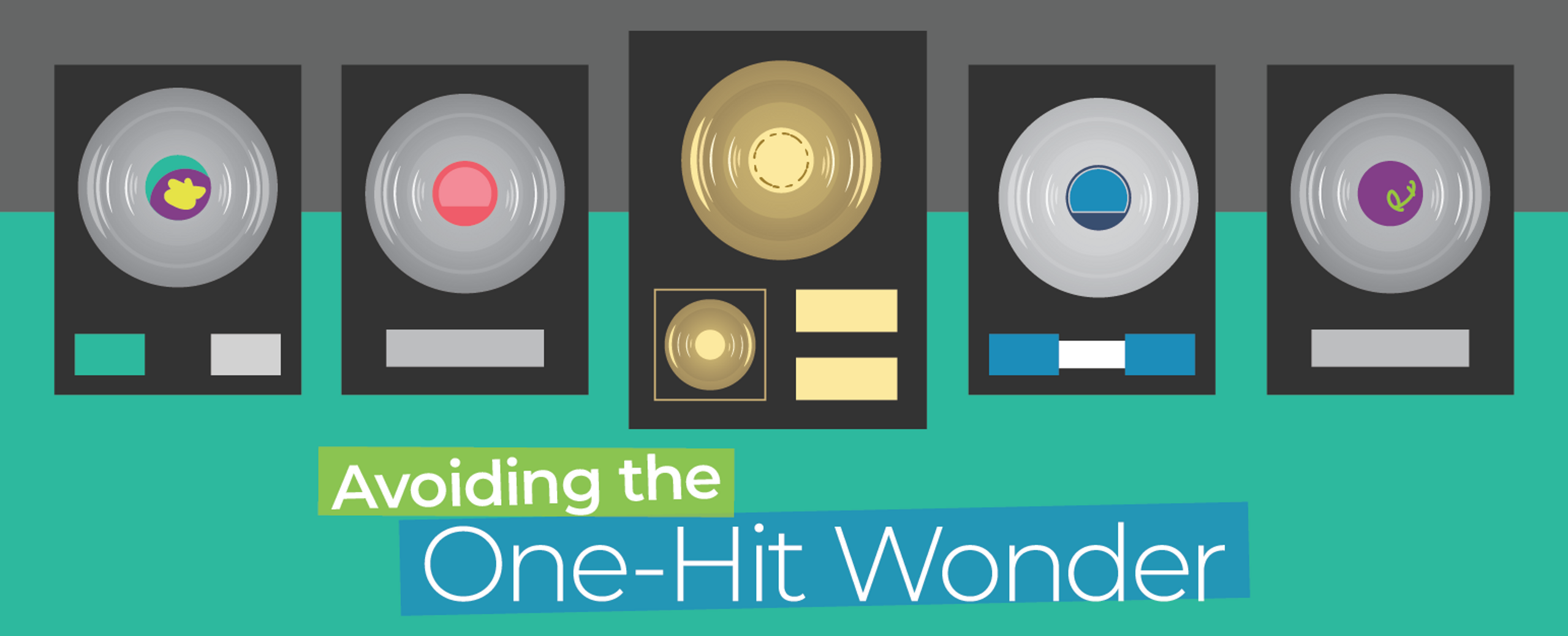
Finding a cure for "one-and-done syndrome"
September 15, 2021Perhaps the easiest step in the continuous improvement process is celebrating the success of a project with measurable improvements and the collective sense that the struggles, even failures, along the way were worth it. Who doesn't love an excuse for an offsite lunch or happy hour?
Unfortunately, one of the hardest parts of developing a continuous improvement culture comes immediately after the celebratory toast: making sure the win just clinched is one of more to come, not just a "one-hit wonder". All you fans of "Tainted Love" know how sad it is when there's no follow-on hit. Indeed, one of the most persistent problems that continuous improvement‐focused organizations face is what can be called "one-and-done syndrome." Usually, the real intention of organized process improvement is to sustainably change the culture of the organization. When an investment to train employees in the tools and methods of Lean/Six Sigma produces initial success, it's certainly valuable, but it's not enough. The objective is a consistent and sustained culture of problem solving — a wall of platinum records produced over many years, not just a lone top 10 single.
An initial mistake companies often make in their eagerness to scale up a continuous improvement initiative is to assume that a large number of trained employees will inevitably yield solid prospects for sustainability. Employees' training, however, is only as valuable as the projects that they are pulled into. MoreSteam CEO Bill Hathaway recommends a clear initial focus on "right-sizing" training by first assessing strategic imperatives, performance gaps, and the resulting project priorities. True to lean thinking, the pull signal from prioritized projects should inform decisions about the training needed to build capability among the required teams.
"The last thing you want to do is train more people than you can support with meaningful project work," Hathaway said. "Process improvement projects must be viewed by leaders as the mechanism by which leaders can achieve their objectives." Projects cannot be something extra, outside of the flow of normal important work. "If leaders don't view projects as the important work necessary to achieve strategic imperatives, then you can end up with newly trained ‘belts’ looking for projects, and often picking the wrong things to work on. The projects should pick the people, not the other way around." The real secret to solving the "one and done" problem is that leadership pull, along with ongoing coaching support.
The primary metric is project success, not the number of people trained.
Projects flow from strategic priorities to close important performance gaps.
Projects pick people; belts don't pick projects.
Project work and the teams doing that work need ongoing support from leaders, including proactive coaching.
Want to learn more?
Check out more content from MoreSteam below and to the right. If you need help structuring a systematic approach to process improvement, or designing a training model that works, call us. We love to talk about this stuff.
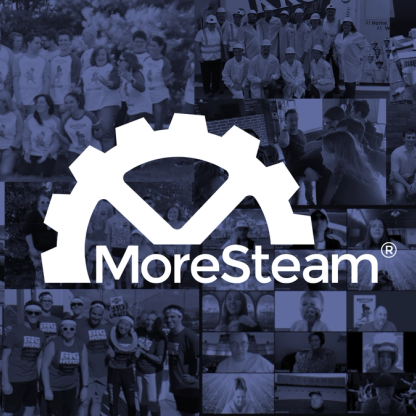
MoreSteam's Enterprise Process Improvement platform includes the tools, training, and software you need to transform your organization, large or small, into a problem-solving powerhouse. Our products are trusted by over half of the Fortune 500 and by other organizations and universities worldwide. When you partner with MoreSteam you gain a team dedicated to helping you succeed.