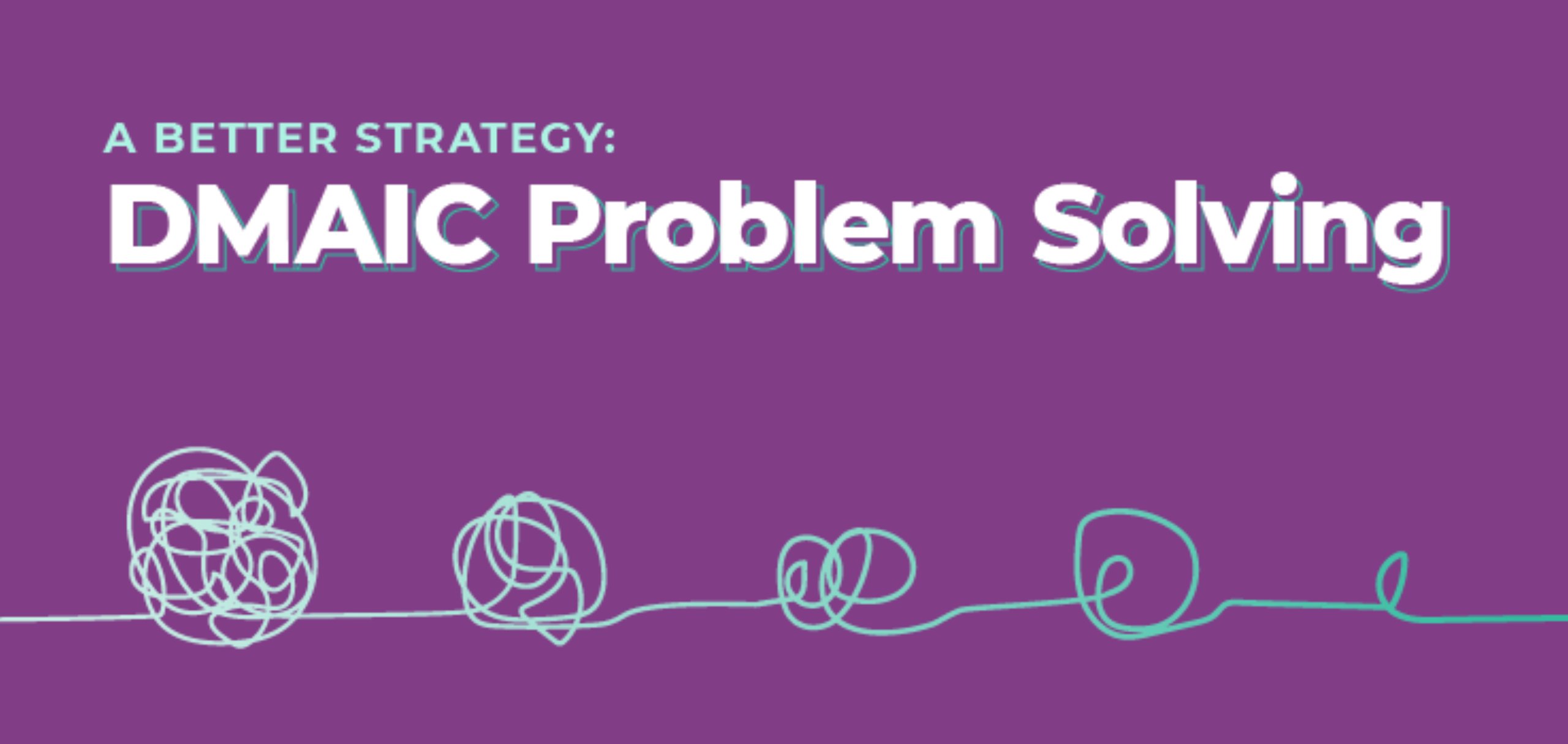
What is the DMAIC Methodology?
September 14, 2022You likely won’t get far into your belt or Lean Six Sigma training without hearing the term ‘DMAIC.’
DMAIC, an acronym for Define, Measure, Analyze, Improve, and Control, is a data-driven method for solving problems, typically in the form of process improvement ‘projects’. First applied to processes on the factory floor in the manufacturing industry in the 1980s, it has since been used successfully in healthcare, finance, technology, and service industries.
While there are several other roadmaps for problem-solving in the Lean Six Sigma universe, like PDCA (or Plan, Do, Check, Act), DMAIC is commonly used for Green Belt and Black Belt process improvement projects.
The DMAIC methodology is a process performance tool that uses statistics and data to help improve current workplace procedures.
DMAIC is an acronym for Define, Measure, Analyze, Improve, Control, and is rarely a linear process.
Each DMAIC phase plays a critical role in the project management process; sometimes more than once.
So When Do You Use DMAIC?
As long as measurable data exists, DMAIC is a good candidate for approaching a process problem. A few examples of problems that would make great candidates for DMAIC improvement projects include:
- Improving customer satisfaction
- Reducing defects
- Reducing variability within processes and in process output
- Eliminating overproduction and excess inventory
DMAIC is a comprehensive problem-solving approach driven by asking the right questions in the right order and employing tools to answer those questions with the goal of eliminating waste and defects in processes.
Each phase has its own questions to ask and tools to use. It is also not a one-and-done solution to process problems. The phases of DMAIC can be employed cyclically. Complete a DMAIC project to improve the baseline performance of a process, then progress through the roadmap again to further improve that new baseline.
How Do You Choose Which Problem to Solve?
Within your organization, it’s doubtful that you would only have one problem that needs solving. Some guidelines to keep in mind when deciding on a new process improvement project include:
- Prioritize the existing processes, challenges, or setbacks your business faces and tackle the most important one first.
- Make sure that the project aligns with the organization’s imperatives.
- Identify who the customer is and what the voice of the customer is. This exercise is how all Lean Six Sigma projects begin.
Let’s dive into the individual steps of DMAIC and explore how each phase is critical to your operational excellence and the success of your improvement projects.
The Define Phase
The first step of the process is to define the problem. Take a step back to establish the magnitude of the problem, whom it impacts, at what frequency it occurs, and the conditions in which it arises.
Consider using the following questions to develop a clear direction for your project:
- Who is the customer?
- What is important to the customer?
- Why are we working on this project?
- What is the scope of this project? Is it broad enough to be important but narrow enough to be doable?
- What is the current process, and why do we need to improve it?
Standard tools used in the Define Phase include process maps, project charter, customer surveys, affinity diagrams, and Gantt Charts.
The Measure Phase
If define is the project planning phase, the Measure Phase is for figuring out how to accurately assess process performance and determine how much of a gap needs to be closed.
Measurements are going to drive your entire Lean Six Sigma improvement project. Therefore, knowing what to measure and how accurately you can measure it is essential. In the Measure Phase, you’ll want to ask questions like:
- How is the current process performing?
- What should be the target for success (in the customer’s terms)?
- Have potentially significant process inputs been identified for further screening?
- What is the data collection plan for all of the above?
- Is the measurement system capable of providing valid and reliable values with an acceptable degree of error?
- Are there opportunities for “quick hits” to realize immediate improvements?
The Measure Phase is also an excellent opportunity to pause and implement any possible short-term containment actions to prevent customers from experiencing defects while project work is underway to resolve root causes.
Standard tools used in the Measure Phase include Measurement System Analysis, Statistical Process Control (SPC), Data Collection Plan, Throughput Yield, and Process Capability.
The Analyze Phase
The Analyze Phase is when you will identify and test underlying root causes of process variability. The whole point of a DMAIC project is to sort through the ocean of process inputs to identify the few truly significant inputs that can be adjusted to achieve a more desired output.
Understanding root cause starts with drawing upon experience and process knowledge to develop hypotheses about the relationship between causes and effects. You’ll develop theories of causality and confirm or discard them based on data and testing.
Use the following questions to guide you in this phase:
- What are the significant inputs, or “X’s”, affecting the output, or “Y”?
- Are those significant input processes stable and capable?
- What are the underlying sources of process variability?
- What levels of those inputs, or “X’s”, will optimize performance?
- Have alternate methods or approaches been validated as effective?
Standard tools used in the Analyze Phase include cause and effect diagrams, hypothesis testing, design of experiments, and multiple regression analysis.
The Improve Phase
The Improve Phase of DMAIC is when you’ll turn analysis into action and implement corrective decisions. And as enticing as it can be to finally solve problems, this can be a challenging phase, as both processes and people often resist the change that improvement requires.
In the Improve Phase, you will:
- Identify, evaluate, and implement process improvements.
- Implement short-term countermeasures.
- Identify and address unintended consequences of improvement actions.
Use these questions to guide you through the Improve Phase:
- What improvement actions are necessary to achieve targeted performance levels?
- Have you established a process to track implementation?
- Are there any obstacles to improvement? What about unintended consequences?
- How might the current system push back?
- Have you evaluated improvement action alternatives?
Standard Tools in the Improve Phase include continuous flow, quick changeover, pull scheduling, and FMEA.
The Control Phase
The Control Phase is the final step in a process improvement project and is arguably the most challenging step to implement. But it is also the most critical.
Once you have implemented corrective actions, the Control Phase verifies results and ensures changes are sustained. This phase often requires people in your organization to change their behaviors and procedures. Anticipating resistance to change and engaging in purposeful change management can alleviate many of these difficulties.
During this phase, you'll want to:
- Verify corrective actions and validate any new measurement systems.
- Track the new process capability.
- Document and share best practices and lessons learned.
The Control Phase is also a chance to reflect. What did you learn? What worked well? What could use further improvement? Are current practices being monitored and improved over time? Are people able to see that data?
Standard tools in the Control Phase include the control plan, statistical process control, process capability, 5S, and visual management.
The Bottom Line
DMAIC is a powerful roadmap for applying Lean Six Sigma to a wide variety of process problems. Rooted in data and guided by organized critical thinking and common sense, this process has resulted in countless successful projects across all industries.
For more information on methods and processes like the DMAIC method, check out our toolbox.
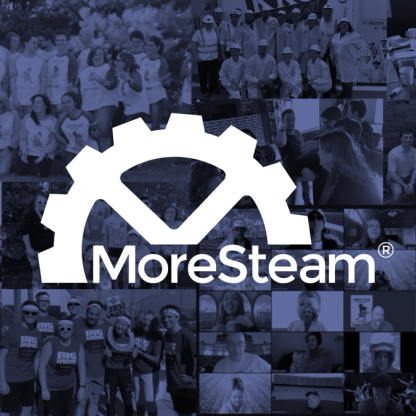
MoreSteam's Enterprise Process Improvement platform includes the tools, training, and software you need to transform your organization, large or small, into a problem-solving powerhouse. Our products are trusted by over half of the Fortune 500 and by other organizations and universities worldwide. When you partner with MoreSteam you gain a team dedicated to helping you succeed.