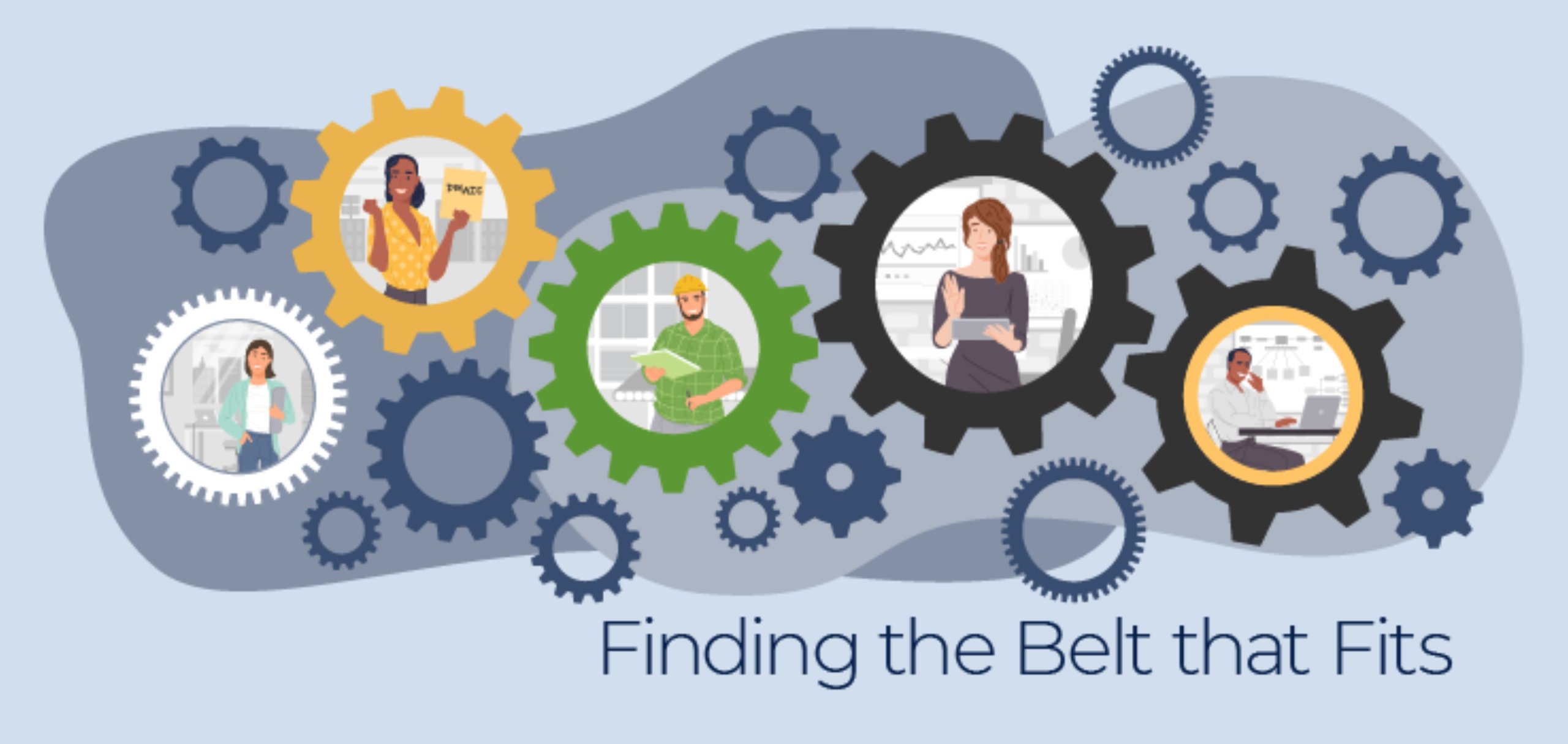
Lean Six Sigma Belt Levels Explained
March 14, 2022At first glance, Six Sigma training can feel overwhelming, especially when trying to decide which belt level is right for you. However, with a basic understanding of the belt levels and their unique functions, the process becomes much clearer—and each level can help elevate your career.
If you’d like to learn more about Lean Six Sigma and its principles, read about it in our "What is Lean Six Sigma?" blog.
As you advance in belt level, you sharpen leadership skills and build technical capability.
Not everyone needs to be a Black Belt. Figure out the right amount of training for you based on the problems you need to solve and your career path.
Each belt level, regardless of color, allows you to bring more value to your workplace.
From a business perspective, creating a culture of organizational excellence depends on aligning training with specific roles and project needs. Every level offers valuable insights, and selecting the appropriate training for employees should depend on the complexity of the problems they are expected to solve.
So what is Six Sigma training? At its core, it's disciplined problem solving. The more complex the problem, the more sophisticated the tools necessary to solve it. Lean Six Sigma follows the DMAIC method. This is an acronym for Define, Measure, Analyze, Improve, Control. This method is one of many taught and followed by MoreSteam, global organizations, and leading universities. Once you understand DMAIC, you’ll start to see problem-solving in a whole new way.
When it comes to process improvement, everyone has an opinion about the best way to get started. If you're not sure what to believe or what your options are, keep reading. Lean Six Sigma is just an approach to problem solving and there are lots of ways to get started.
Below is a basic guide to the MoreSteam Six Sigma belt levels and the unique skills each one brings to the table.
White Belt
The White Belt level of Six Sigma training provides a foundational understanding of basic problem-solving principles. Training at this level is all about awareness—getting employees to think critically about current workplace processes and consider ways to improve them. White Belt training is a great starting point for learning key terms and concepts.
Yellow Belt
A Lean Six Sigma Yellow Belt provides a foundational understanding of essential Lean Six Sigma concepts and tools. Typically requiring around 20–30 hours of training, Yellow Belt education covers topics like the 5 Lean principles, process and value stream mapping, error-proofing, and more.
Yellow Belts are equipped to participate in projects as team members, often under the guidance of a Green Belt. They may also engage in quick-hit kaizen events, which require focused effort over several days to solve pressing issues. Additionally, Yellow Belts help address smaller, local process improvements that don’t require advanced statistics.
Project Examples for Yellow Belts:
- Typical Yellow Belt Project: Yellow Belts often support quick process improvements, frequently in Kaizen events, such as reducing wait times in a specific department or assisting with minor adjustments to improve efficiency.
- Real-World Example: See how Mercy Ships used Yellow Belts in value stream mapping to improve efficiency and support their mission of providing free medical care.
Green Belt
Building on the fundamentals of Yellow Belt, Lean Six Sigma Green Belt training provides a deeper dive into Lean Six Sigma concepts and practices.
Green Belt training is ideal for those aiming to lead projects, covering everything learned at the Yellow Belt level with added material. Topics include communication, hypothesis testing, Statistical Process Control (SPC) charts, and more advanced tools. Green Belt training typically requires around 80 hours of comprehensive study.
Once fully trained, Green Belts are equipped to lead their own DMAIC projects. They also receive leadership training to manage small project teams, often working with other Green Belts or Yellow Belts. With more in-depth analysis skills, Green Belts gain a solid grounding in statistical methods, enabling them to tackle complex process improvements.
Project Examples for Green Belts:
- Typical Green Belt Project: Green Belts frequently lead departmental projects, such as streamlining a manufacturing process to reduce waste and increase efficiency.
- Real-World Example: Discover how Medtronic applied Lean Six Sigma techniques to redesign its value stream maps, leading to significant enhancements in its manufacturing processes.
Black Belt
Lean Six Sigma Black Belt training requires a significant commitment beyond the Yellow and Green Belt levels, making it ideal for those pursuing leadership roles in project management and process improvement.
Typically requiring around 140 hours of in-depth training, Black Belt training covers advanced topics like Design of Experiments (DOE), advanced hypothesis testing and managing complex process improvement projects and teams. It also includes all foundational material from the Green and Yellow Belt levels.
With this extensive training, Black Belts are equipped to lead advanced projects involving complex statistical analysis and Designed Experiments. Black Belts receive training in both technical and leadership skills, enabling them to mentor others and confidently guide teams of Green Belts in achieving project goals.
Project Examples for Black Belts:
- Typical Black Belt Project: Black Belts are prepared to handle cross-departmental projects involving complex data analysis, such as improving supply chain logistics or optimizing resource allocation across multiple teams.
- Real-World Example: Discover how Habitat for Humanity-MidOhio used Black Belts to streamline donation processing, reducing the time from receipt to display and boosting revenue to support affordable housing initiatives.
Master Black Belt
The Master Black Belt level represents expertise in operational excellence. Building on the foundation of previous belt levels, Master Black Belt programs prepare professionals to lead complex, enterprise-wide projects, develop the technical and process improvement skills of teams, and support organizational transformation at the executive level.
As a highly regarded and sought-after qualification, Master Black Belts are experienced Black Belts who have undergone extensive advanced training in design, statistics, and modeling. They often lead large-scale process improvement initiatives and play a crucial role in coaching Black Belts and Green Belts through projects and leadership challenges.
Project Examples for Master Black Belts:
- Typical Master Black Belt Project: Master Black Belts oversee strategic initiatives that align with company-wide goals, such as driving continuous improvement across all departments or supporting executive-level decision-making with advanced analytical insights.
- Real-World Example: Learn how the YMCA of Greater Cincinnati leveraged a Master Black Belt to lead a comprehensive restructuring project during the COVID-19 pandemic, ensuring continued service to the community.
But Which One is Right for Me?
No matter the belt level you choose for your role, your career will benefit. Point blank, everyone benefits from understanding the basics. But how far you go in your training will depend on your ambition, role and responsibilities.
If you're an organization looking to introduce Lean Six Sigma into your workplace, we recommend a "just-enough" approach to training until your project efforts yield returns. It doesn't make sense to have everyone trained as a Green Belt. Varying certifications among employees ensures that you have enough support at each level and all participants are sufficiently coached and mentored. Plus, it guarantees that projects are overseen, maintained, and successfully completed.
Green Belt and Yellow Belt training are valuable career boosters for process or manufacturing engineers, continuous improvement specialists, and project managers. For those aiming for senior director or project manager roles, Black Belt or Master Black Belt training may be more suitable. Consider your role, career goals, and specific responsibilities to decide which belt level aligns best.
Also recognize that Lean Six Sigma Training requires time to learn and practice the skills. You might decide to start at a lower level and work your way up. There is no wrong answer, and each level brings added value to your career and workplace. For more information on the various belt levels that MoreSteam offers, and how they can each add value to your career, check out our course catalog.
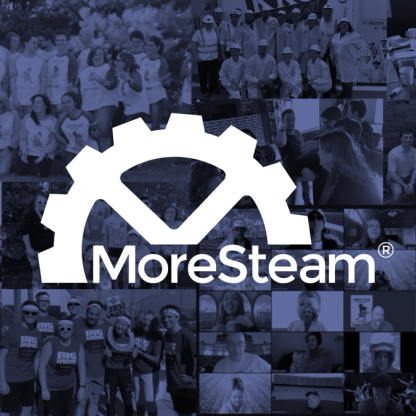
MoreSteam's Enterprise Process Improvement platform includes the tools, training, and software you need to transform your organization, large or small, into a problem-solving powerhouse. Our products are trusted by over half of the Fortune 500 and by other organizations and universities worldwide. When you partner with MoreSteam you gain a team dedicated to helping you succeed.