
A Voyage of Continuous Improvement: Transforming Operations at Mercy Ships
With years of experience in Continuous Improvement roles, Chris Gresens joined Mercy Ships as their first Director of Continuous Improvement just two years ago. And while standing up an operation certainly poses its challenges, in his short tenure Chris and his team have made incredible strides toward adopting a culture of operational excellence across the organization.
For more than 40 years, Mercy Ships has been providing hope and healing around the world.
Mercy Ships is a non-profit organization that provides free surgery and medical training to regions with scarce resources. They travel coast-to-coast on large converted “hospital ships,” serving those needing life-changing medical care…all through their extensive network of volunteer medical professionals.
Mercy Ships has been incredibly successful in pursuing its organizational mission of providing hope and healing to the world. But as long as children and families are still waiting for care, the efforts don’t stop. So, when the COO was tasked with standing up operations on a second ship, he recognized that it was imperative to replicate predictable, efficient processes, especially when the people in the process were constantly changing.
We had the pleasure of sitting down with Chris and chatting about his experience with Mercy Ships, from his initial rollouts to his vision for the organization’s future.
The interview has been edited for length and clarity.
Tell us a little about the beginning stages of your journey at Mercy Ships. What were a few process improvement methods that you used right away?
Overall, my strategy consisted of three components:
- Practical process mapping and improvement. For component one, I facilitated the development of functional maps and value stream maps of different departments across the organization. These maps were used to clearly identify the areas that needed process improvement based on Lead Time / Processing Time and percentage Complete & Accurate - a risk rating by the GAO, and captured by the SMEs who own those areas.
- Organizational outreach. Component two consisted of setting up an org-wide community of practice. I implemented monthly virtual meetings that discuss major process improvement topics and help connect process-focused folks across the org.
- Formal training. For component three, I wanted to provide formal training and certifications to begin embedding the knowledge within teams and give the participants something to use in their careers moving forward.
What was your roll-out plan for training people in the company?
Through the use of our COP (Communities of Practice), we began offering Lean fundamentals. Then, we extended Yellow Belt training to those who wished to continue to receive more Lean training.
In terms of shepherding a group of people in the continuous improvement mindset, you want the best quality training.
How did the training impact the culture of Mercy Ships?
We had the training going, and we received regular interest from probably 5-10 enrollees every month in Lean Fundamentals, with roughly 10% of them wanting to inquire more about Yellow Belt. But when we lost one of our specialists running the program, the faucet shut off, and there was an immediate impact because the training wasn’t available for almost a whole quarter. People were inquiring, wondering, ‘What is going on?’
So we recently restarted it and were able to pick it back up this month [January]. We actually just sent out our enrollment form for Lean Fundamentals and had about 20 people enrolled in one day.
We also put out a survey about community practice and what topics they wanted covered, and we received a very, very high response rate on the survey. It showed recognition of terms; people wanted to know more about continuous improvement and learn more about DMAIC; they wanted to continue to build a community across departments to see what other people are doing and compare their methods with theirs to improve their process effectively.
Within our finance department, we’ve constructed Value Stream Maps, and that’s a huge step in the right direction. Not only have they constructed VSMs, but through the training, community practice, and the relationships we’ve built, they are stepping into a level that we’ve wanted to see where you have these leaders that create these maps with our department. Then, they go and present those maps to their leaders. That’s a huge leap forward. We now have key stakeholders willing to step forward and use the terminology and process maps to talk about their process with their leaders and develop strategies for 2024.
That’s big because I just did a SWOT analysis yesterday for our department, and one of the major weaknesses was people investing the time and then letting the work go. Our finance department is investing the time and carrying the work forward, so that’s a really big accomplishment right there.
What made you choose MoreSteam as your training program?
The answer is easy. When you’re standing up a practice within a major multinational organization and building a team from the ground up, it’s difficult to take the time to create training material to spread the culture and education needed for CI to take hold. I had the opportunity to partner with a professional organization that provides the highest level of continuous improvement training. It’s approachable by someone who’s brand new, but also can take a seated professional and give them new material they’ve never seen before – that is why I knew MoreSteam would be the right option.
It was very easy to compare MoreSteam to the other certifying bodies across the map in terms of the quality. I could pay $400 to take a test today, or I could be mentored and work with a professional body to get the training over a long period of time – you can pick one or the other.
In terms of shepherding a group of people in the continuous improvement mindset, you want the best quality training.
I also had prior experience with MoreSteam while working at Southwest Airlines. I participated in the Zombie Hunter simulation , which was one of the first steps that I took that helped me break out of the academic to a practical exercise. Even though it’s fantasy, it’s still a practical exercise where you can see some of the work and the data sets you capture and what they look like when they’re actually put into a semi-real-world example.
The Zombie Hunter simulation directly displayed the quality of working with MoreSteam, of the one-on-one attention you get whenever you engage them and partner with or purchase their services.
What challenges or setbacks did you face that you did not anticipate?
As director, I continually advocate to ensure CI recommendations are integrated into the overall strategic direction or strategic vision of senior leadership. In terms of an area or challenge that we didn’t anticipate, it’s the continued advocacy we have to provide to ensure that a CI mindset is used and integrated into the development of our overall strategy.
I just did a SWOT analysis, and one of the major weaknesses was people investing the time and then letting the work go. Our finance department is investing the time and carrying the work forward, so that’s a really big accomplishment.
What are some of the most significant impacts you’ve seen since rolling out your CI initiatives?
The largest impact we have seen since rolling out CI at Mercy Ships is implementing a current state mapping requirement for all Project Management Office projects. In a nutshell, any department that wants to press forward with a major technological change or initiative must work with the CI team to properly capture the current state mapping of all processes involved and develop a problem statement before submitting a business case to the PMO.
Tell us about the second ship and how that has impacted your initiatives.
With a second ship, it is vital that operations run smoothly and in a rhythm. Because of the distance between teams, one focus of our work is breaking down the walls between them. We need both ships to have the same process across marine operations, human resources, supply, medical ops, etc., so the crew can seamlessly work at each ship.
What does the future look like in terms of projects? What’s your one-year plan? Five-year?
Our plan for the next year is to follow a major initiative called Streamlines Success. This project aims to identify areas for improvement, map operations, and assist department leaders in developing improvement plans to lean out their processes and increase operational efficiency. Over the course of the next five years, we will be steadily working toward standing up independent CI practitioners within each department and supporting data-driven decision-making and process improvement.
Any closing thoughts?
All in all, it has been an exciting journey so far. Some days, it’s an uphill battle and other days, we can’t seem to stop winning. With the strategic partnership we have built internally with senior leadership and the external partnership built with MoreSteam, Continuous Improvement at Mercy Ships will continue to be a key player in delivering life-saving surgery to those in the world without access.
Christopher Gresens is the Director of Continuous Improvement for Mercy Ships. Previously, he was a Business Analyst at Southwest Airlines, where he earned his Lean Six Sigma Green Belt certification. Chris has extensive experience leading and facilitating subject matter experts through the phases of DMAIC and Kaizen projects. He uses his project management skills via Lean Six Sigma to successfully achieve data-driven change. Chris earned his Bachelor of Science at Texas Christian University and his MBA at the University of Texas at Arlington.
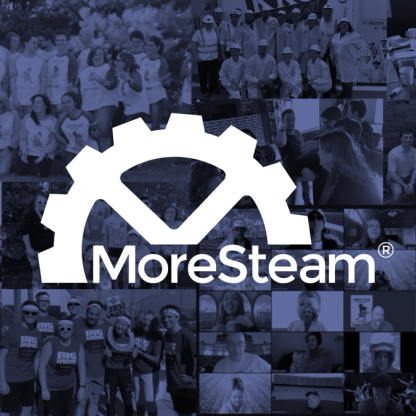
MoreSteam's Enterprise Process Improvement platform includes the tools, training, and software you need to transform your organization, large or small, into a problem-solving powerhouse. Our products are trusted by over half of the Fortune 500 and by other organizations and universities worldwide. When you partner with MoreSteam you gain a team dedicated to helping you succeed.