
What is a Lean Six Sigma Green Belt?
A Lean Six Sigma Green Belt is a professional qualification that signifies training in Lean Six Sigma methodology, equipping individuals with tools and techniques to enhance efficiency and productivity within an organization. Green Belts spearhead improvement initiatives, navigating them through the DMAIC process to streamline operations and reduce waste. Their ability to accurately identify problems and critically evaluate potential solutions is crucial in driving improvements that directly impact efficiency, quality, safety, and the bottom line.
A Green Belt can come from a wide variety of backgrounds and industries — Finance, HR, Manufacturing, Sales — all areas of a business can use a process improvement roadmap such as DMAIC or PDCA to solve problems better. Many companies invest in Lean Six Sigma Green Belt Certification for individuals to build strong problem-solving tools to apply in their area of expertise within the organization.
Green Belt Quick Facts
Average Salary: Green Belts earn $119,758* annually, depending on industry and experience.
Cost Savings: Green Belts can save companies $250,000* or more per project by reducing waste.
Belt Level: A Green Belt is an intermediate Six Sigma level, positioned between Yellow and Black Belt.
*As of 2024, reported in 'Salary by highest Six Sigma Belt—U.S. and Canadian respondents',' Quality Progress, December 2024.
Green Belts on the Job
What type of project work is expected from a Green Belt?
A Six Sigma Green Belt is expected to lead improvement projects and support Black Belts and Master Black Belts as part of a team on more complex projects on complex initiatives, applying the DMAIC roadmap to solve real-world problems. Typical project work revolves around solving problems that the customer and the organization care about. Improvements in safety, quality, lead time, and cost are all examples of metrics Green Belt projects may target.
Improvements in products, services, experiences, and environments can all be measured with a combination of quantitative data and qualitative customer feedback. For example, an electronics company might use product sales to test the appeal of its newest accessories, or a restaurant chain might gather input from its wait staff and customers to determine the best parts of its latest menu. Regardless of industry, a certified Lean Six Sigma Green Belt can make a substantial impact by applying tools like Kaizen for continuous improvement, root cause analysis to uncover underlying issues, and process mapping to visualize and optimize workflows.
Key Skills and Competencies of a Lean Six Sigma Green Belt
Green Belts are equipped with a range of skills and tools to drive process improvements and foster a culture of continuous improvement. From root cause analysis to running a Kaizen, they apply practical methods that create lasting impact in their organizations.
Critical Thinking
Breaks down complex problems and implements solutions
Process Mapping
Analyzes process sequences to identify problems
Statistical Analysis
Utilizes tools like EngineRoom to make data-driven decisions
Root Cause Analysis
Identifies underlying issues to prevent recurring problems
Kaizen
Promotes a culture of small, ongoing improvements
Team Building
Facilitates collaboration between team members
SIPOC
Create project charters to define inputs and outputs
Error Proofing
Prevents a process from producing defects
Industries and Career Paths for Green Belt
Lean Six Sigma Green Belt skills are applicable across diverse industries, from healthcare to technology. These roles enable professionals to drive quality, efficiency, and cost savings within their organizations.
- Healthcare: Focused on streamlining processes, Green Belts work to enhance patient care, reduce inefficiencies, and improve resource management, directly impacting quality and operational performance.
- Finance: In finance, Green Belt skills are applied to optimize workflows, allocate resources effectively, and elevate client satisfaction through smoother, more efficient processes.
- Manufacturing: Within manufacturing, Green Belts play a crucial role in reducing waste, refining quality control measures, and supporting efficient, cost-effective production practices.
- Technology: Green Belts in tech enhance team productivity, streamline complex workflows, and use data-driven strategies to lead impactful improvements in operations.
- Retail and Customer Service: In retail and customer-facing roles, Green Belts elevate customer experience by refining processes, ensuring consistency, and enhancing service quality.
What to Look for in a Lean Six Sigma Green Belt Course
Choosing the right Lean Six Sigma Green Belt course goes beyond cost, time commitment, or the credential itself. The real measure of a quality training program is in the lasting knowledge and confidence it builds in participants. Upon completing a Green Belt training program, participants should be able to apply the DMAIC methodology to define and analyze a given process problem and ultimately find an effective improvement to implement, including effecting the right change management to sustain the solution.
Training Formats for Different Learning Styles
- Self-Paced Online: Ideal for independent learners, this format lets you progress at your own speed, exploring course materials and case studies at your convenience.
- Blended Learning: Enjoy the best of both worlds with a combination of self-paced study and live instruction, designed to deepen understanding and enhance skills.
What Does it mean to be Green Belt Certified?
Unlike some certifications, Green Belt certification standards are not universally set. At MoreSteam, certification requires not only passing a rigorous exam but also successfully completing a Green Belt project that demonstrates your ability to apply Lean Six Sigma principles in a real-world scenario. Graduates receive a printed certificate and a digital badge to showcase their achievements.
Key Takeways for Green Belts
- Responsibilities: Green Belts lead process improvement projects and contribute to larger initiatives within their organizations.
- Core Skills: Mastering problem definition, process mapping, statistical analysis, and change management.
- Industry-Wide Demand: Green Belts are in demand across industries like finance, HR, engineering, healthcare, and IT.
- Career Growth and Benefits: Certification can open doors to career advancement, higher salaries, and valuable project experience.
- Confidence in Application: MoreSteam training empowers you with the skills and confidence to drive meaningful change.
Advance Your Career with MoreSteam's Green Belt Courses
At MoreSteam we offer several Green Belt courses, each built with the same high-impact and practice-based course content, just delivered to you differently based upon your unique learning needs. Select a course below to learn more and explore each Green Belt course further.
Want to Learn More About Lean Six Sigma? Curious About the Other Belt Levels?
Lean Six Sigma is a journey of continuous learning and growth, with each belt level offering unique skills and opportunities. If you're curious about how the Green Belt fits into the bigger picture or want to explore Lean Six Sigma in more detail, check out these resources:
What is Lean Six Sigma?: Discover the core principles of Lean Six Sigma and how it transforms organizations through continuous improvement.
Lean Six Sigma Belt Levels Explained: Discover how each level builds on the last and where the different belts fit into the continuous improvement process.
What is DMAIC Methodology?: Learn about the structured problem-solving process at the heart of Lean Six Sigma.
The History of Lean Six Sigma: An insightful interview exploring the origins and evolution of Lean Six Sigma.
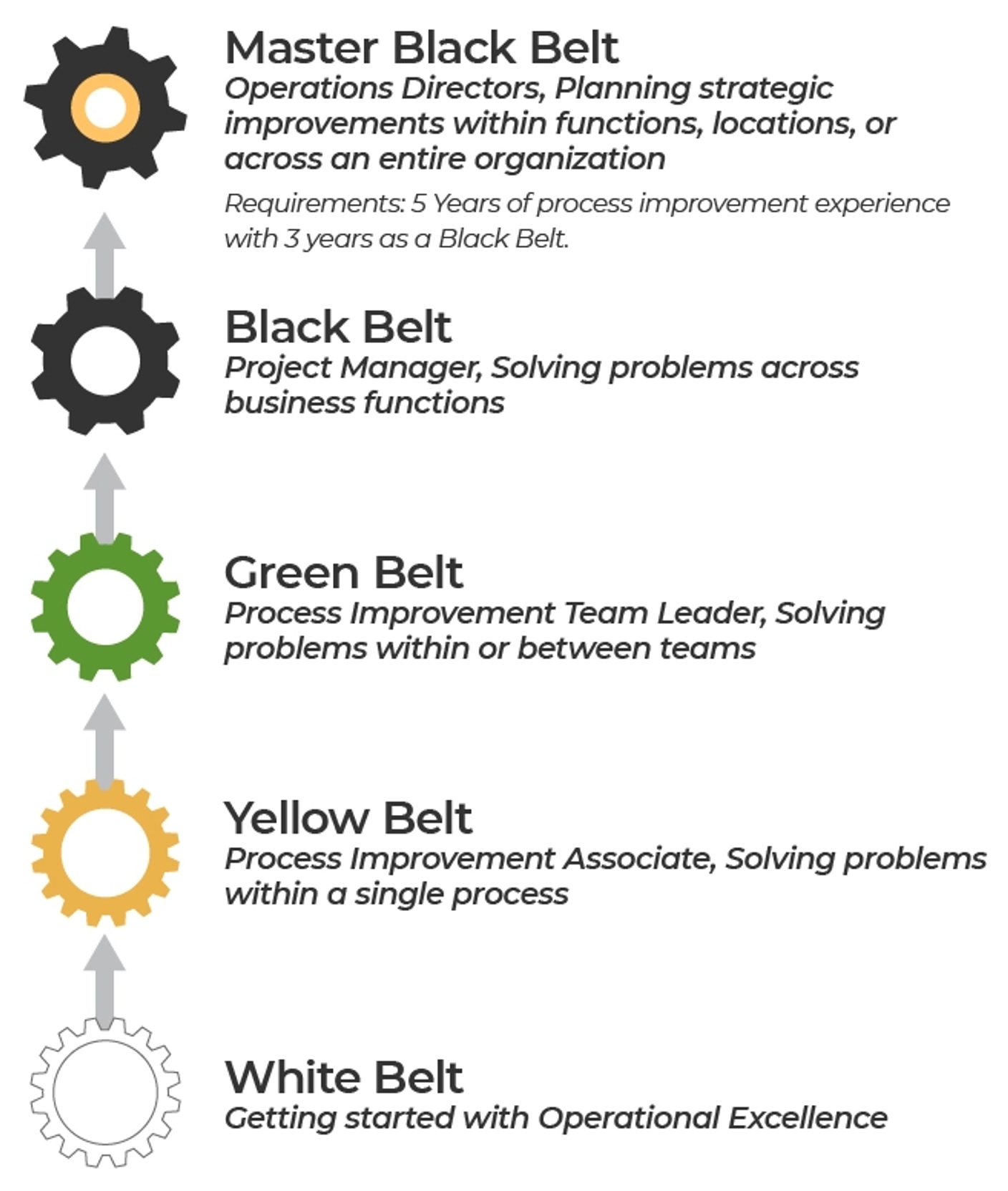
Additional Resources for Lean Six Sigma Green Belt
Frequently Asked Questions
Still have questions? We're here to help.
614-602-8190
No Robots. Only humans.
support@moresteam.com
You'll still get a human here, too.