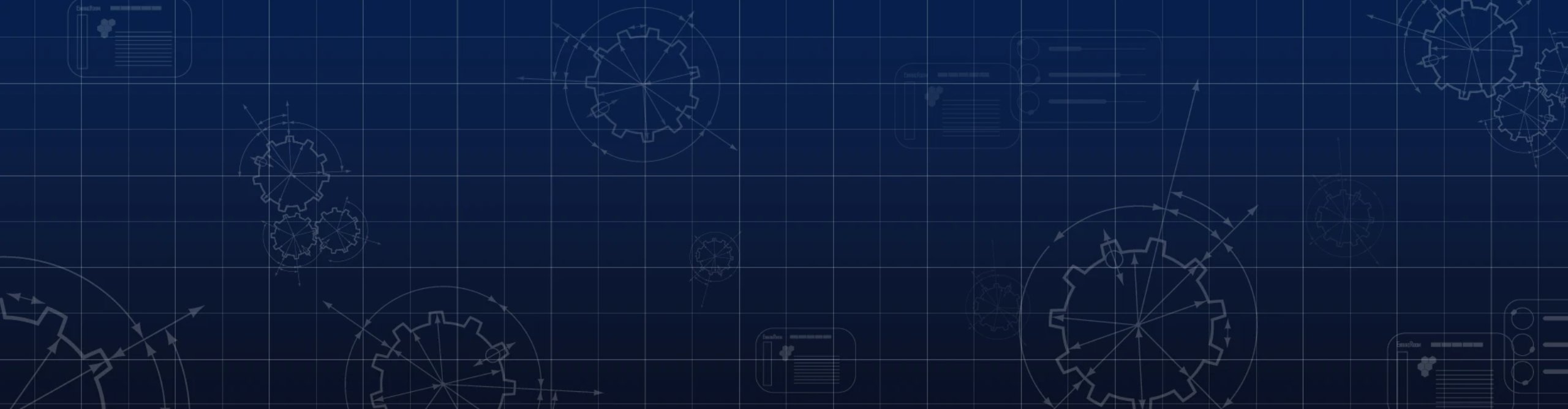
From Aspirations to Achievements
October 24, 2017In mid‐September, we were very happy to host our 15th annual Best Practices Conference at Ohio State University. Thinking back on the first gathering back in 2002 at Rolls‐Royce in Indianapolis, we've all come a l‐o‐n‐g way. The "Best Practices" of 2002 were mostly aspirational; there were nice theories about how to blend digital technology with people into new structures for learning and doing, but little actual evidence to prove success. Now the successes are real and replicable.
We're learning how to better employ technology to support the people doing the work of process improvement in durable, sustainable models. One great example is Cardinal Health, which has used organized process improvement to generate over $1.8 billion in economic benefits over the last dozen years ago. Yes, that's billion with a B! But it's not just large corporate enterprises that are employing process improvement methods in new and creative ways, and it's not all about saving money. We also heard from the Habitat for Humanity of Mid‐Ohio, which is using a people‐centric approach to build on team strengths and significantly improve the output of new housing.
Process Improvement Without Boundaries
One common thread among those organizations with successful process improvement activities is their pragmatism: they start with a clear idea of the necessary problems to be solved, followed by the practical application of only those tools and methods demanded by the questions to be answered. Purists may be horrified, but lean projects are using DMAIC as an organizing roadmap and even employing statistical analysis…and more classic "six sigma" projects are keeping things simple and focusing more on speed of execution.
In the last few years, there's been a lot more tailoring of approaches, curriculum, teaching methods, and support structures to meet the specific needs of the enterprise. Six sigma had developed a bad (but earned) reputation for long cycle times to execute DMAIC projects, as if the M stood for Months instead of Measure. Some of this was driven by a desire to use tools in order to use tools — perhaps a good practice for learning, but certainly not a good practice to show results quickly. More recently there's been a tilt back toward question‐driven project work rather than tool‐driven work, and a much‐needed focus on simplification and sense of urgency. In the lean domain, it seems that some of those who were tempted to "just do lean" because it is more organic and relatively simple (look, no math!) have recognized that the world is increasingly data‐rich and sometimes more complex methods are required to solve more complex problems.
And for all the shortcomings of organized process improvement, there is a lot of evidence that disorganized process improvement does not work better…so the only option is to stick with it, experiment, learn, and revise.
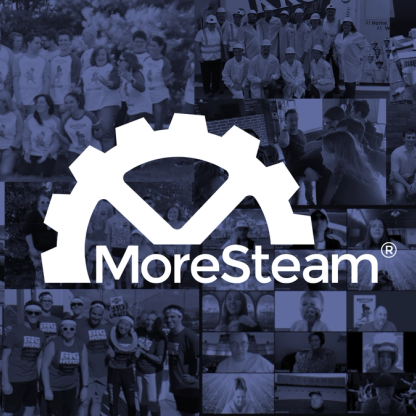
MoreSteam's Enterprise Process Improvement platform includes the tools, training, and software you need to transform your organization, large or small, into a problem-solving powerhouse. Our products are trusted by over half of the Fortune 500 and by other organizations and universities worldwide. When you partner with MoreSteam you gain a team dedicated to helping you succeed.