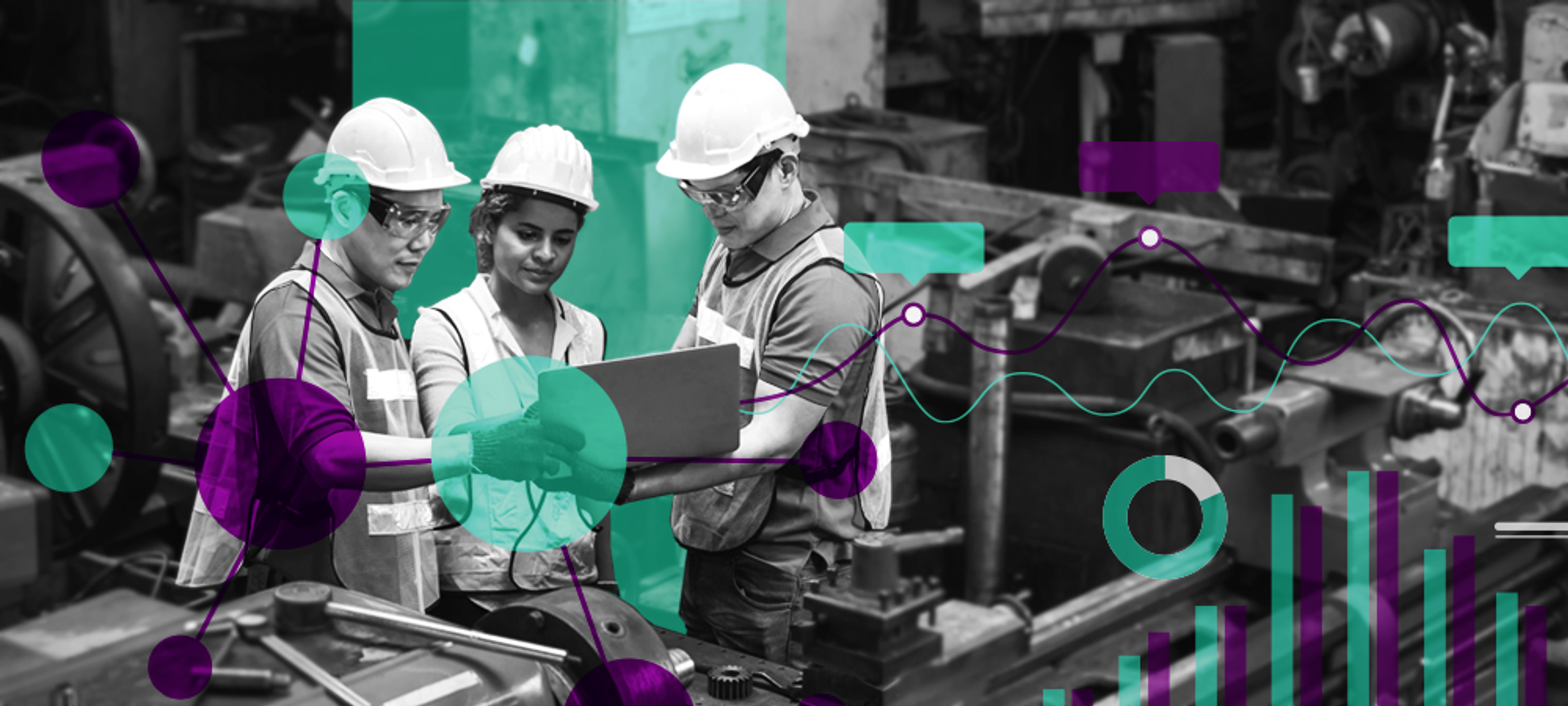
In Praise of Unglamorous Activities
June 10, 2024The world is seemingly awash in glamorous people taking part in glamorous activities: professional athletes competing in sports, fashion models walking the runway, Hollywood celebrities attending endless award shows, T.V. personalities hosting almost anything, social media influencers creating "content," the idle rich indulging in conspicuous consumption, and elites attending swanky gatherings in Davos. They serve a purpose, but the important machinery that sustains our daily lives and keeps the world's gears turning depends on decidedly less glamorous work.
In the operational universe of getting important things done, unglamorous people doing unglamorous work grow food and deliver it, build the products everyone relies upon, run the power plants, construct the buildings, fix the roads, maintain the airplanes, nurse our injuries, teach our children, and tend to the remaining often-overlooked and annoying details that are necessary to make complex systems actually function.
The foundational activities necessary to drive out process waste and improve quality are critical to satisfying customer requirements. I think we would all agree that no business can survive for long, let alone prosper and grow, without satisfying its customers. The relationship between satisfied customers and business success is well-established. And yet, however critical they may be to organizational success, the unglamorous activities at the heart of operational excellence are often out of fashion because, for one thing, they are unglamorous. They are not easy. They are not quick. They cannot be faked. And they are sometimes painful. And we cannot "clever" our way out of doing this unglamorous work.
Product and process quality are suffering
The erosion of corporate willingness to do the hard work of process improvement is like an athletic team without the drive to train and practice. Hope for success is a much easier strategy than training for success, but hope alone doesn’t work, and we are all experiencing the consequences of a diminished leader-led process improvement work ethic as quality levels for many important products have suffered in recent years. By now, everyone knows about Boeing’s persistent (endemic?) quality issues. Those problems are dramatic, but Boeing is not alone.
Let’s examine some imperfect but available data to assess the broad state of the quality world…
The following chart shows automotive recalls in the U.S. market over the last two decades. In spite of all we’ve learned about designing and managing for quality, the number of recalls has marched steadily upward.
More alarmingly, the advent of electric vehicles has brought new problems linked to the new technology. The chart below shows the number of vehicle recalls accompanied by “Do not drive” or “Park outside away from structures” advisories — totaling over 4.7 million vehicles in 2023. It’s a sobering picture.
Turning to other consumer products, the U.S. Consumer Product Safety Commission reported a consistent 15-year decline in product recalls until a recent spike.
In the calendar year 2023, airlines operating in the U.S. posted a mishandled (including lost) baggage rate of 0.58%. A rate below 1% doesn’t sound too bad until you consider the volume: 0.58% equates to 2.4 million mishandled bags out of approximately 420 million total bags transported. For any given flight of 200 or more people, that means one passenger is not reunited with their luggage upon arrival.
Certainly, many, many products and services are produced and delivered at near-flawless levels of quality. To a large extent, we’ve all come to take high quality for granted, and since quality is a function of expectations that change (usually increase) over time, the bar is constantly being raised. Many products and services are remarkably good, as many producers have taken full advantage of advanced automation, digital prototyping, 100% testing, and machine learning to fine-tune methods. We have all raised our expectations accordingly. That makes producers with poor quality stand out.
I’m sure I’m not alone in experiencing widespread service quality issues since the pandemic. The attitude in many restaurants, hotels, and other labor-intensive industries seems to be, “We’re doing the best we can... we can’t find enough staff... so just deal with it”.
Managers at all levels and across industries are understandably frustrated with labor shortages. That’s fair. But sometimes, those shortages also reveal fundamentally poor process design, which is a management responsibility. Poor process design can contribute to avoidable work task stresses that make the work unattractive, further exacerbating the labor problem. A stronger focus on service quality through robust process design could have provided more resilience to labor shortages that have exposed underlying process problems while inflicting bad experiences on customers. As Deming said, “A bad system will beat a good person every time.” We seem to see many of those “every time” outcomes.
And then there’s healthcare. Who doesn’t have a horror story about errors and bad service in healthcare?
Painful Lessons Learned
For those of you who are old enough, you may remember the pervasive sense of angst about quality and competitiveness in the U.S. in the late ‘70s and into the ‘80s. Speaking from my own experience, the quality of manufactured products was terrible. I bought my first new car during that period, and the Pontiac dealer told me, literally, “Drive it a bit and write down all of the things that are wrong with it, then bring it back, and we’ll fix them all.” Poor quality was an expectation. In 1980, an NBC News special called “If Japan Can, Why Can’t We?” showcased W. Edwards Deming’s thinking on statistical approaches to quality improvement and became a national call to action of sorts.
People started listening to Deming’s message, and many took action. For context, here’s one of Deming’s core messages from Out of the Crisis:
“Support of top management is not sufficient. It is not enough that top management commit themselves for life to quality and productivity. They must know what it is that they are committed to – that is, what they must do. These obligations cannot be delegated. Support is not enough: action is required.”
That’s how it went through the ‘80s and ‘90s. Sometimes, the message didn’t click right away. It was hard and uneven work, but organizations were making progress. I saw this firsthand, although…starting from a baseline of automobile instrument panels being kicked into place on an assembly line (true story), there was nowhere to go but up.
Statistical quality improvement methods became widely adopted, and the Lean methods of the Toyota Production System became widely emulated. In the mid-’90s, Motorola, Allied Signal, and GE created a closer linkage between operational excellence and financial performance, and profits are strong financial pheromones. Senior leaders supported and engaged with process improvement, and for a while at least, the work was glamorous (well, sort of). In many respects, it was a quality renaissance.
But quality improvement is kind of like a weight loss program: it’s very easy to drift back into bad eating habits, and much of the quality world seems to have drifted.
Why?
Why has quality slipped in so many places over the last decade? Here are some theories based on my experience and recent observations of the world:
Complexity: Products and their supply chains have become more complicated. All things being equal, higher complexity means more points of failure, and more possibilities for failure generally means more failures. Complexity is the natural enemy of quality.
Product Pace: Product life cycles have shortened. This puts a premium on good design because there’s less time to find and fix problems. The pandemic and global conflicts crushed many supply chains, leading to all sorts of messy transitions, relocations, and substitution of inputs, sometimes without adequate validation. As it turns out, the world is not flat.
Attitudes: Two rapidly spreading conditions called “Landscaper Syndrome” and “Gembaphobia” have infected leaders and led to their disassociation from process improvement work. Landscaper Syndrome is the belief that you can just hire someone to do the dirty work for you. For some activities, you can do that. Senior leaders probably don't need to be intimately involved in calculating international transfer payment taxation. But, they do need to be intimately involved in the core value-creating processes of the organization. That means not being afraid to go to where the work is actually done (“Gemba” in Japanese) to see the actual process and talk to the actual people doing that work. Jim Womack coined the term “Gembaphobia” to describe this affliction.
Preparation: Are quality methods and process improvement techniques part of the core curriculum at most business schools? Analytics has certainly become a popular topic, and that should help improve quality, but only if systematically applied to solve operations problems. Overall, business schools don’t appear to have a strong operations focus. It is too often assumed that “operations people take care of that quality stuff."
Short-Term Focus: Finance folks are running the show in a lot of places. There’s nothing wrong with finance folks per se, but good financial evaluation is based on operational evaluation because financial metrics are an outcome; they are an evaluation of operational performance. They don’t exist in isolation. Unless the firm is a financial institution, the fundamental value-creating activities of the enterprise are not financial. It’s a pretty basic requirement, I think, that the people running the show ought to have a very solid grounding in how, exactly, real value is created by the enterprise. Financially-driven short-term time horizons can lead to bad long-term operational decisions, including a failure to recognize the total risks of poor quality.
Desire for Instant Pudding: And most of all, quality improvement can be hard, unglamorous work. Leaders are always faced with pressing, fast-changing, and sometimes conflicting demands for their attention. There have also been plenty of more interesting shiny objects to chase recently, all with a “power pill” appeal: RPA, big data analytics, design thinking, and AI.
These newer technologies can accelerate quality improvements if harnessed to pull in that direction. But quality excellence requires more than an investment in technology. Quality excellence requires capable and collaborative problem-solving that cuts across organizational boundaries. And quality excellence is built on true leadership engagement: setting priorities, making hard choices, and the patience and persistence to stick to those priorities over time, even in the face of short-term financial pressures.
Building a sustained and sustainable quality culture requires demonstrated constancy of purpose over years.
Steven Spears, the author of “Decoding The DNA of the Toyota Production System,” said the best predictor of success in establishing the Toyota Production System (TPS) among Toyota suppliers was the extent to which the organization’s leaders actively engaged in teaching TPS principles within their organization. I think this finding holds across industries and process improvement approaches.
The first two problems mentioned above are largely environmental, so they are not controllable, but the remaining four problems can all be solved by leadership choices.
The State of Quality Leadership
The American Society for Quality Excellence (ASQE) recently conducted a survey on the global state of quality, and the results regarding leadership reveal and predict the quality problems highlighted earlier. Only 43% of the survey respondents completely agree that company leaders have prioritized quality, and only 31% agree that leaders are actively involved in quality programs.
This is only one survey, so there is a risk of overgeneralizing. Still, the results have been consistent over the last three years and are consistent with my own anecdotal observations of the quality practices at large multinational companies. The most senior executives responsible for quality tend to have less organizational standing than they used to. They are down a rung or two in the organizational hierarchy: Chief Quality Officers have become Vice Presidents of Quality or Vice Presidents of Operational Excellence, and VPs of Quality or Operational Excellence have become Directors.
It’s not true across the board, but it seems to be a trend. Those who were once charged with building systems of operational excellence, reporting at a very senior level, are now redirected to coordinate operational excellence training within the HR organization. That’s a symptom of the “Landscaper Syndrome” I mentioned previously.
The Path Forward
The good news, if there is good news, is that there are no mysteries. The cause-and-effect model between leadership actions and product quality performance is well understood. We’ve been through this before, and we’ve fought back successfully. Everything that Deming taught us 40 years ago still holds. Here’s a classic quote;
“An important obstacle is the supposition that improvement of quality and productivity is accomplished suddenly by affirmation of faith. Letters and telephone calls received by this author disclose the prevalence of the supposition that one or two consultations with a competent statistician will set the company on the road to quality and productivity – instant pudding. ‘Come, spend a day with us, and do for us what you did for Japan; we too wish to be saved.’ And they hang up in sorrow. It is not so simple: it will be necessary to study and to go to work. “
Collectively, we know exactly WHAT to do; now, we need to decide that we WANT to do it. Leaders need to fully engage in process improvement activities. There is no wonder drug for quality health, only sustained unglamorous work to teach and lead data-driven, structured problem-solving across the enterprise and then do it again, day after day after day.
It’s time to get serious and do that work.
References
- U.S. Department of Transportation
- "2023 IoE Benchmarking Highlights Report." ASQ Insights on Excellence, 2023.
- Consumer Product Safety Commission
- The American Society for Quality Excellence
- "NHTSA 2023 Annual Report Safety Recalls." National Highway Traffic and Safety, March 2024.
- "Statement of Commissioner Peter A. Feldman: Record Recall Numbers Reflect Return on Investment for American Consumers." United States Consumer Product Safety Commission, November 01, 2023, cpsc.gov.
- Murray, Teresa. "Safe at Home in 2024?" U.S. PIRG Education Fund, March 7, 2023, pirg.org.
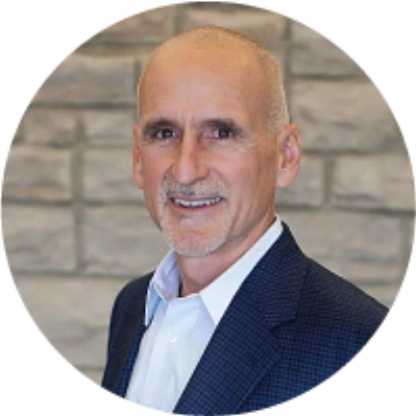
CEO • MoreSteam
MoreSteam is the brainchild of Bill Hathaway. Prior to founding MoreSteam in 2000, Bill spent 13 years in manufacturing, quality and operations management. After 10 years at Ford Motor Co., Hathaway then held executive level operations positions with Raytheon at Amana Home Appliances, and with Mansfield Plumbing Products.
Bill earned an undergraduate finance degree from the University of Notre Dame and graduate degree in business finance and operations from Northwestern University's Kellogg Graduate School of Management.