Restock Inventory
Restock Inventory of Items with Replenishment Pull. At a coffee shop, as your coffee bean supply runs low, replenish with new bags of beans.
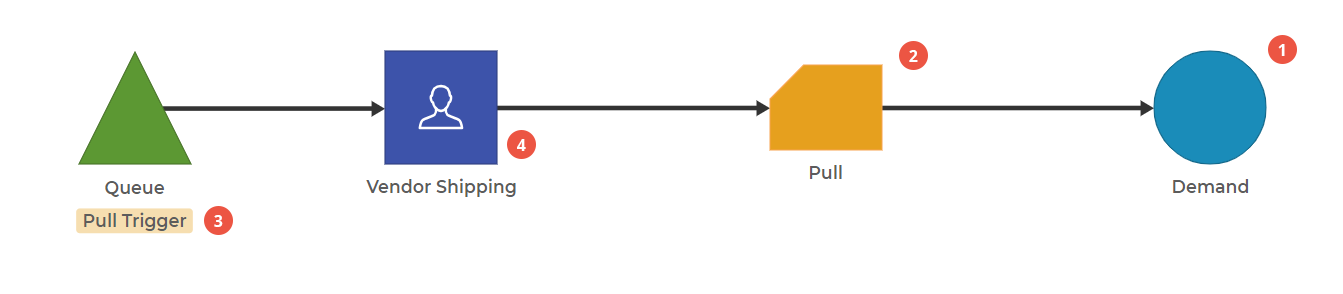
1. Create Pull Demand. Adding a demand block to the END of a process makes it act in pull mode. It will generate demand that pulls items from upstream blocks.
2. Size your system. The Replenishment Pull block holds items like a Queue Block, but when it gets down to a certain number of items, it triggers more items to be created at another block. Selecting the correct parameters is called "sizing" the pull system. To size your system correctly, consider the time between order and arrival, the amount of safety stock you want on hand, and the order size you would typically put in based on the demand.
3. Identify the Block where new items are created. The Trigger label shows where the new items will be created as batched items. The batch containing the correct items is created at the Queue Block when the trigger occurs. These items can be the same as the items that are held in the Pull Block, or they can be different items.
4. Model the Lead Time to receive the order. After the batch item is created in the Trigger Block, it moves through the connected process. In this case, a simple Activity Block represents the shipping time for the ordered items. Because we're dealing with a batch item, use the "Setup Time," which adds a single amount of time for the entire batch, and a "Processing Time" of C(0).
This model shows a Lean Replenishment Pull system. Think of this model like you would baby diapers. You never want to run out of diapers, but you only have so many places to put them all. So you limit your inventory and order more when it makes sense. This model allows you to experiment with the right levels to ensure your needs are always met.
Was this helpful?