Restocking Parts
Restocking Parts. This is one way of modeling a resource whose responsibility is to keep workstations stocked with materials and tools, ensuring operators can work without interruption. In this case, the restocks happen on a pull-basis.
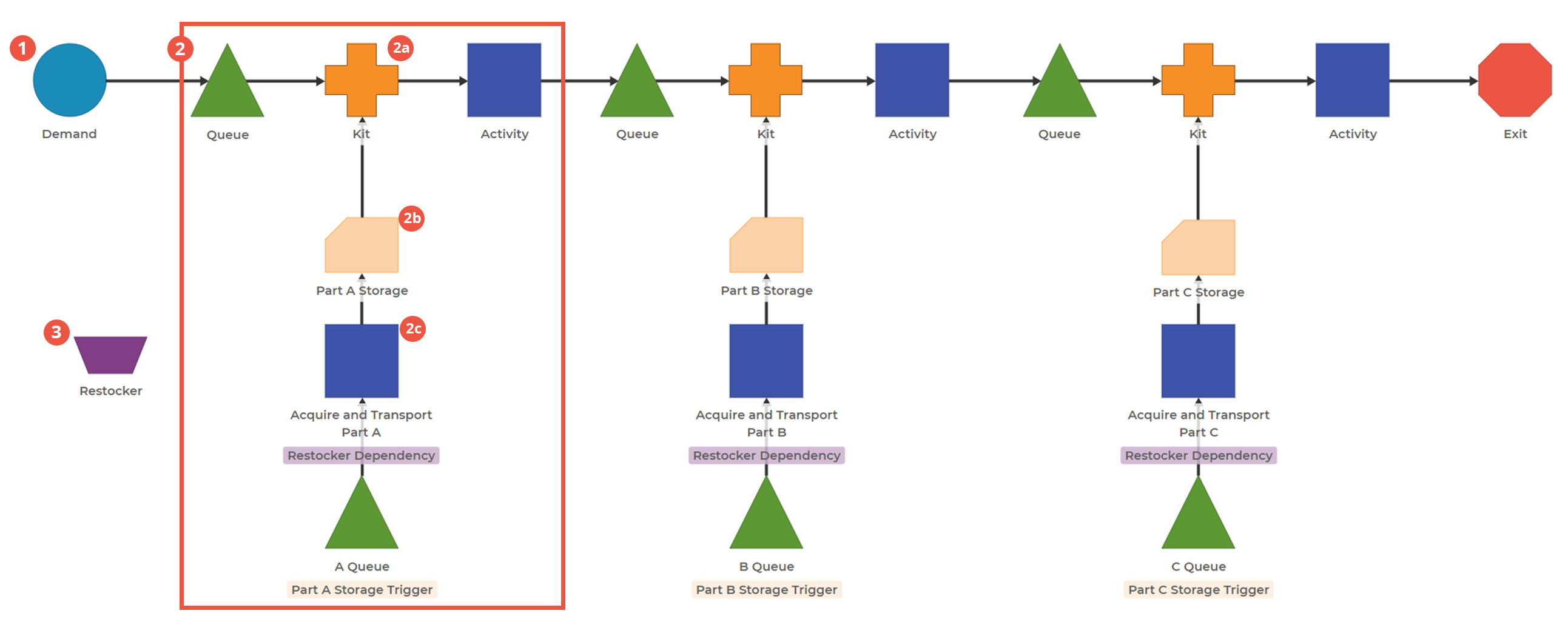
0. This model has seven items: Order, Part A, Part B, Part C, Order+A, Order+A+B, Order+A+B+C. Order+A is made of Order and Part A, Order+A+B is made of Order+A and Part B, and Order+A+B+C is made of Order+A+B and Part C.
1. Generate Demand for the Production Process. Set the rate of demand at the beginning of the manufacturing process.
2. Note these activities are repeated three times. 2a. This Kit Block combines the previous item and a Part from Storage to make a new item. The following activity block represents an operator's time to perform this action.
2b. Parts are pulled from storage, diminishing the supply. Because this is a Replenishment Pull Block, when the supply reaches the minimum (trigger point), an order will generate at the Queue Block labeled with the Trigger.
2c. The Activity Block models the activity time of the restocker acquiring and transporting the parts. The Activity Block has a label indicating it has a Restocker Dependency. Parts will only move from their respective Queues when the Restocker is available to complete the activity.
3. The Restocker Resource is shared across the three 'Acquire and Transport' activities. By having a single Resource Block responsible for all three activities, you can effectively model the time spent by the Restocker on restocking.
This model can help size the Storage for each part by reviewing the results to see when there are stockouts. In addition, it can help model how the transportation time might affect the effectiveness of the Restocker. This is an intial take on modeling a water-strider; we will show another version next week!
Was this helpful?