Work Cell (Factory in a Factory)
Work Cell: Also called a "Factory in a Factory," the items that go through the Work Cell all follow the same path through the process with a similar load at each step. In this process, items move through three machines, where an operator loads and unloads those machines.
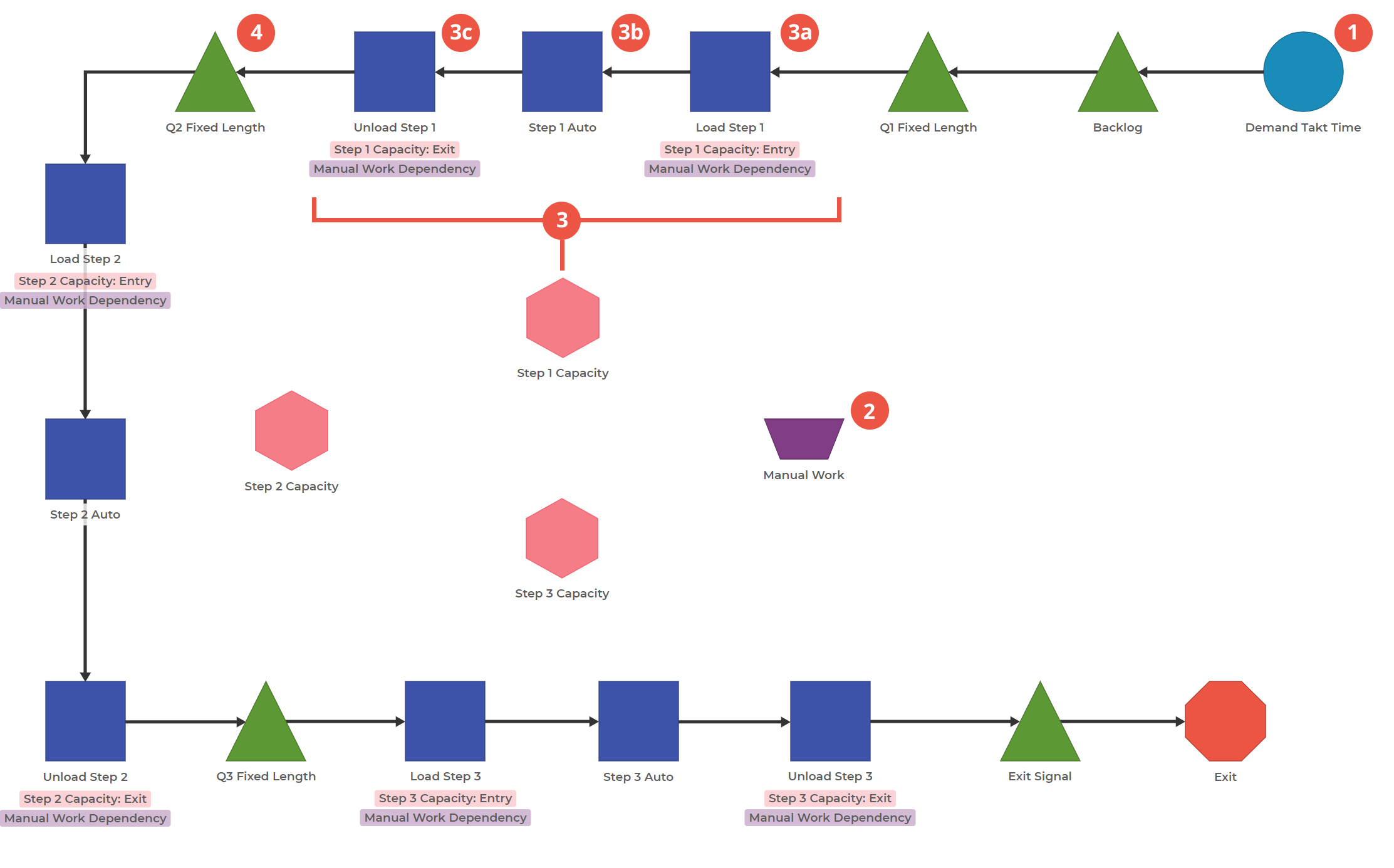
0. Two Item Types: It is important to note that this model has two different item types. In this case, they're "Item 1" and "Item 2."
1. Set Demand for Each Item: Item 1 has more demand than Item 2.
2. Introduce Manual Labor: This Resource Block represents the worker who will do the manual labor required for this process. Each machine must be manually loaded and unloaded, but you can set a single operator to do all those activities using a Resource Block.
3. Model a Machine: Each set of 3 Activity Blocks and the associated Core Pull Block represents one machine.
- 3a) The first Activity Block represents the time to load and has the Manual Labor Resource Block attached.
- 3b) The second Activity Block represents the time for the machine to do its work. Manual Labor is not needed for this step.
- 3c) The third Activity Block represents the time to unload the machine and has the Manual Labor Resource Block attached.
4. Limit the WIP by Limiting the Queue Lengths: Set the Queue Lengths between machines to be a limited number of items. This accurately represents real life, where a conveyor belt (for example) between the steps has a small and limited capacity.
Ideally, work cells are used for a family of like items where there is little process, demand, and mix variability. A simple spreadsheet model would be all you need in this situation.
However, if your process experiences variability of any sort, a simulation model will help you determine the needed capacity and balance for your process.
Was this helpful?