Store Workshop for Spare Parts
Store Workshop for Spare Parts: This model can help test the stock of supplies in the face of inconsistent demand and lengthy approval processes.
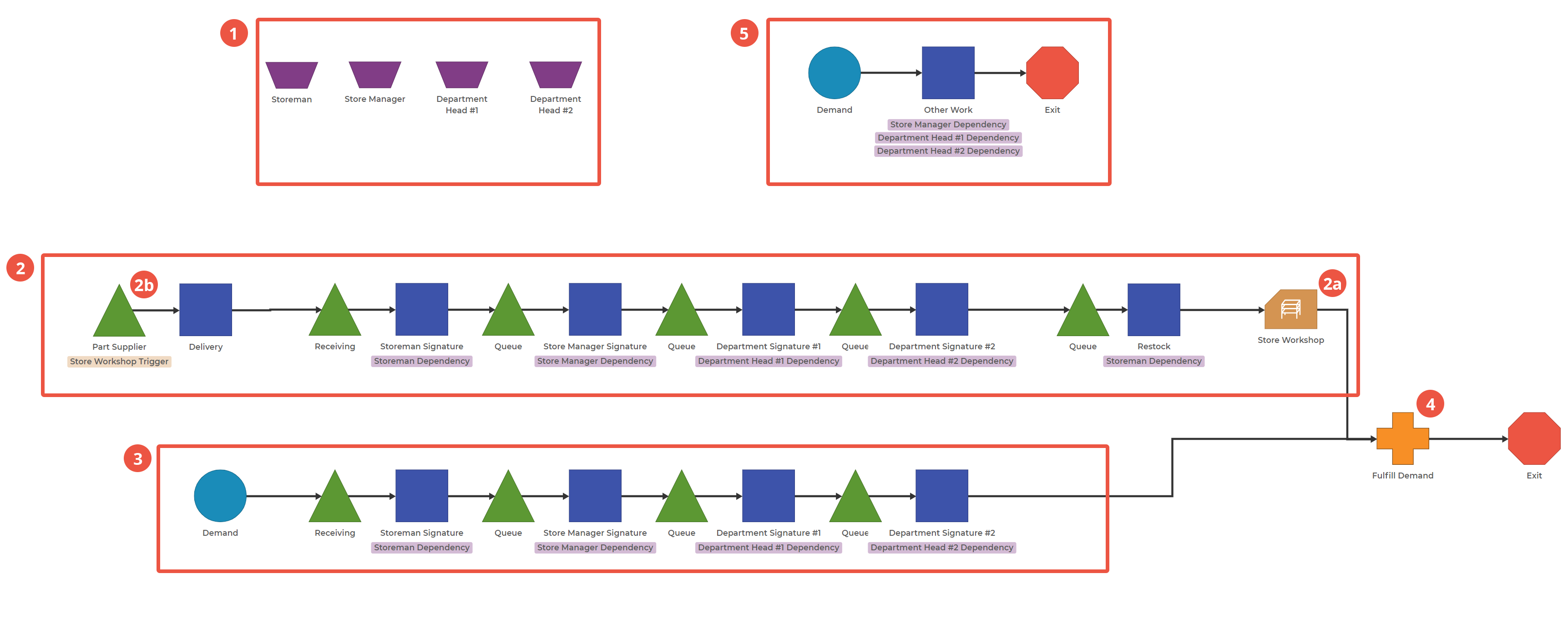
0. There are four items in this model. Request for Part, Part, Fulfilled Part, and Other Work.
1. Create Your Resources. In this model, we want to account for the time of an employee across different parts of the process. This is done with Resource Blocks. In this case, we've created one resource block to represent each worker.
2. The Book-In Process. Start by looking at the Replenishment Pull block (2a). This is the Store Workshop that holds a certain number of available parts. If the supply in this Workshop gets too low, it will trigger an order of supplies to be created in the Part Supplier Queue Block (2b) and subsequently begin the delivery process. The following steps are all the approvals needed for this Book-In process. Note that each Resource block we have previously created is assigned to their respective approval steps.
3. The Book-Out Process. This subprocess begins when a Request for Part comes in, as generated by the Demand Block. Then, a similar approval process to the Book-In process begins. Note again that the resources required are assigned to their respective steps.
4. Fulfill Demand. This Kit Block creates Fulfilled Part items by combining a Request for Part with a Part from the Store Workshop. Because the Part item is marked as "Wait to Pull" in the Item Types window, Parts will wait in the Store Workshop until a Request for Part arrives in the Kit Block. The Fulfilled Part then makes its way out to the Exit Block for use.
5. Establish "Other Work" to accurately reflect time spent on approvals. A key part of this model is this subprocess for Other Work. Since various employees can't dedicate all of their time to one task, the requests will accumulate in the blocks until they are able to complete them. Note how the Store Manager, Department Head #1, and Department Head #2 are all assigned to the Other Work Activity block. When an Other Work item comes in about once every hour, the resources will be "tied up" working on tasks that take between 30 and 200 minutes, preventing them from working on the approval processes.
To create inconsistent demand, the Demand Block in Step 3 can be adjusted for different distributions and time frames and can even create layers by adding multiple "Request for Part" items to this block.
To test for overstocking and understocking, look at the Store Workshop. By adjusting the parameters here, you'll better understand how much supply is necessary to meet the demand.
To adjust the approval processes, take a look at the Queue-Activity combinations in Book In and Book Out processes and see where process improvements might change the Total Lead Time (TLT) of items in the Exit Block.
Was this helpful?